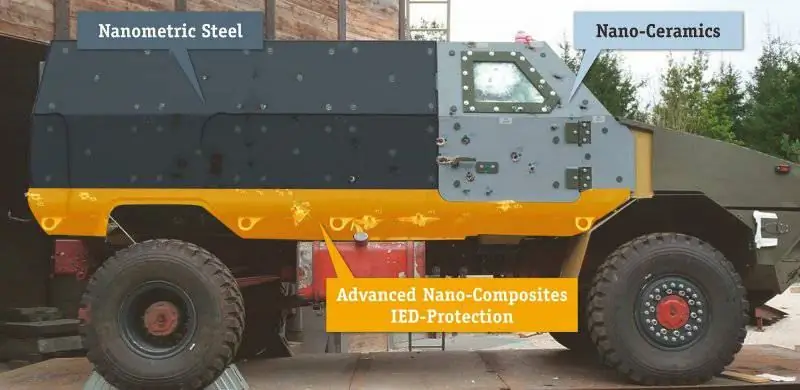
Iveco MPV käyttää uusimpia IBD Deisenroth -suojaratkaisuja, jotka perustuvat pääasiassa nanoteknologiaan
Passiivinen panssari: viimeinen este
Panssaroitujen ajoneuvojen rungot ovat edelleen terästä, johon pultataan lisäpanssarisarjoja. Kuitenkin mitä enemmän perusrakenne voi antaa ballistisen ja räjähtävän suojan kannalta, sitä korkeampi lopullinen suoja on. Lisäksi jopa asennettaessa aktiivisia suojajärjestelmiä, jotka tuhoavat hyökkäävät ammukset jopa lähestyessä, tuloksena olevat suuren energian palaset voivat aiheuttaa vakavia vaurioita ajoneuvolle, mikä taas vaatii hyvää perussuojaa
Ruotsalainen SSAB on yksi panssarimateriaalien tunnetuista asiantuntijoista, ja sen Armox -panssariteräsperhe on tunnettu kaikkialla maailmassa. Perheeseen kuuluu kuusi eri tyyppiä, teräslajin nimitys osoittaa Brinellin keskimääräisen kovuuden. Vaikka kovuus vaikuttaa suoraan ballistiseen suojaan, sitkeyttä tarvitaan räjähdysenergian absorboimiseksi - kaksi ominaisuutta, joita itse asiassa ei voi olla yhdessä. Muovattavuus pahentaa tätä ristiriitaa, koska lujat teräkset ovat yleensä vähemmän muotoiltavia ja niillä on usein ongelmia hitsattavuuden kanssa.
Ajan myötä SSAB -terästen ballistiset ominaisuudet paranivat vähitellen: vuonna 1990 Armox 500T -terästä, jonka paksuus oli 9 mm, tarvittiin M193 / SS92 -ammuksen pysäyttämiseksi 937 m / s nopeudella, mutta kymmenen vuotta myöhemmin Armoxilla 600T -seos, vain 6 tarvittiin pysäyttämään mm. Vielä kymmenen vuotta ja 4,5 mm Armox Advance tekee saman, vaikka luku ei ole enää sen arvoinen, koska kovuus ylittää Brinell -asteikon! Alusta alkaen 70,7 kg / m2 SSAB on onnistunut pudottamaan painonsa 47,1 kg / m2 kymmenessä vuodessa ja 35,3 kg / m2 seuraavan vuosikymmenen aikana. SSAB: n asiantuntijoiden mukaan merkittävää laskua ei odoteta, todellinen luku vuonna 2020 on 30 kg / m2. Yhtiön T & K -osasto pyrkii parantamaan nykyisen materiaalin sitkeyttä ja muovattavuutta enemmän kuin sen kovuutta, varsinkin kun räjähdys on nykyään suurin uhka. Sen Armox 440T 420-480 HB Brinell -terästä on kutsuttu suosituimmaksi energiasyöjäksi, ja sen sitkeys helpottaa minkä tahansa muodon, kuten kiinteän pohjan, saamista. Jopa kovempaa Armox 500T -terästä, jonka kovuus on 480-540 HB, pidetään räjähdyssuojamateriaalina.
Kuten edellä mainittiin, Armox Advancedin pääominaisuus on kovuus, joten SSAB pitää tätä terästä tosiasiallisena keramiikkana. Siksi yhtiö suosittelee voimakkaasti, ettei sitä muovatta tai hitsata, koska sitä ei saa kuumentaa yli 100 ° C: n kovuuden säilyttämiseksi. Kuinka saavuttaa samanlainen suojaustaso ja paino tulevaisuudessa muovattavammilla materiaaleilla, on erittäin vaikea tehtävä tänään.
Uusien panssariterästen joukossa on tietysti huomattava Super Bainite, joka esiteltiin syksyllä 2011. Yhdistyneen kuningaskunnan DSTL Defense Science and Technology Laboratoryn kehittämä uusi teräs valmistetaan Tata Steel UK: ssa. Sen suorituskyky on paljon parempi kuin tavallisella panssariteräksellä. Nämä ominaisuudet eivät ole vain seurausta kemiallisesta koostumuksesta, vaan myös valmistusprosessista, erityisesti lämpökäsittelystä jäähdyttämällä ilma ja sulatetut suolat. Lopputuotteella on kaksi kertaa ballistinen suorituskyky kuin valssatulla homogeenisella panssarilla.
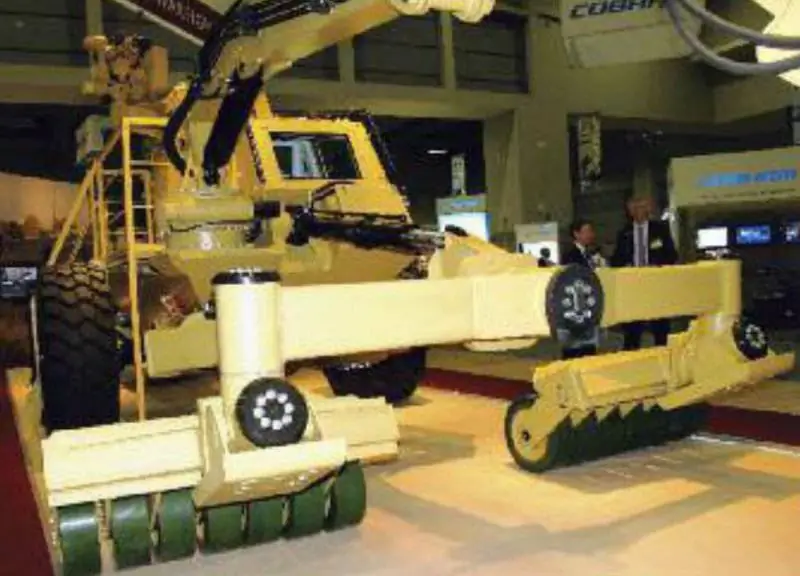
Eteläafrikkalainen Aardvark Perroc käyttää tuotteissaan laajasti SSAB Armox 500 -terästä. Tämä osoittaa, että jopa tämä erittäin kova teräs kykenee absorboimaan suuria määriä energiaa.
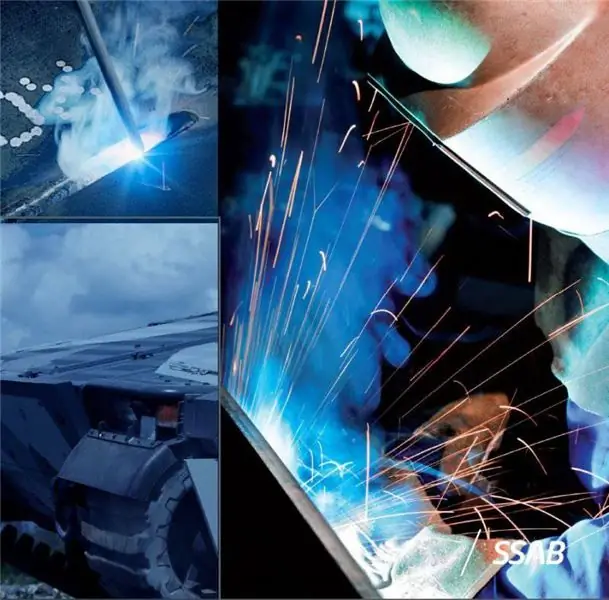
SSAB valmistaa monimutkaisia muotoja Armox 440T -teräksestään, jota usein kutsutaan”energian syöjäksi”. Se sopii erittäin hyvin rakenteille, jotka ovat alttiina IED: lle. SSAB pyrkii parhaillaan tekemään panssariteräksistään muovattavampia.
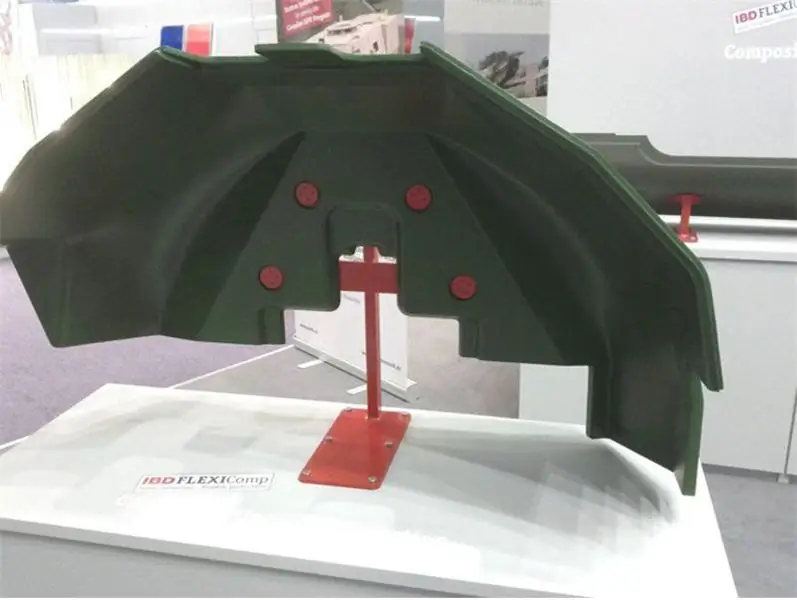
IBD FlexiComp -vuoraus mahdollistaa volumetristen turvaelementtien tuotannon, mikä vähentää heikkojen kohtien määrää koko turvajärjestelmässä
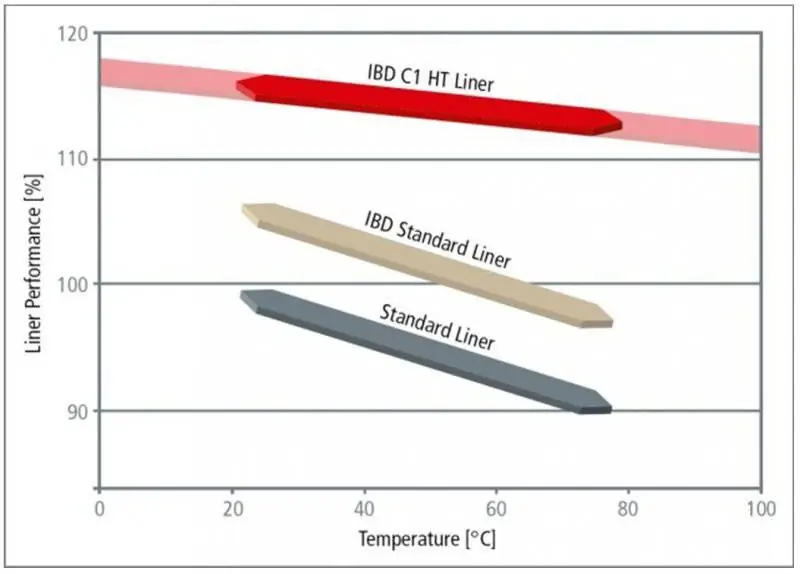
Kaavio IBD -vuorausten ominaisuuksista lämpötilan funktiona. Korkeiden lämpötilojen vaikutus on suuri huolenaihe käytettäessä koneita kuumassa ilmastossa
Joulukuussa 2012 Lockheed Martin UK ja Surreyn yliopisto julkistivat uuden, yksinkertaisemman menetelmän panssaroitujen ajoneuvojen suojan ja selviytymisen parantamiseksi. Tutkijat ovat kehittäneet menetelmän keraamisten materiaalien käsittelyyn parantaakseen alumiinioksidikeramiikan ja piikarbidikeramiikan tarttumislujuutta komposiittialustaan, mikä lisää merkittävästi panssarin lujuutta. Keraamisten levyjen kiinnittäminen taustaansa on aina ollut tämän tekniikan Achilles -kantapää. Tulokset osoittivat, että uusi tekniikka parantaa vetovoimia. Testit ovat osoittaneet, että kun 14,5 mm: n panssaria lävistävä sytytysluoti ammutaan panssarilevyyn, se pysyy ehjänä.
Teknologinen kehitys on edelleen IBD Deisenroth Engineeringin ydinliiketoimintaa, kun taas passiiviset ratkaisut ulkoistetaan tällä hetkellä Rheinmetall Chemprolle, josta 51% on Rheinmetall Defence ja 49% Deisenroth -perhe.
Kun tohtori Ulf Deisenroth kehitti neljännen sukupolven panssariteknologioita erityyppisille materiaaleille, tehtävänä oli vähentää massaa säilyttäen samalla suojaustaso tai päinvastoin lisätä tietyn massan suojaustasoa, kun taas uudet tekniikat lupaavat säästöjä yli 40%. Ne perustuvat uusimpiin läpimurtoihin nanomateriaaleihin liittyvän passiivisen suojan alalla, joihin kuuluvat nanokiteinen keramiikka, nanometrinen teräs ja erittäin lujat kuidut. IBD on kehittänyt yhteistyössä teräksenvalmistajien kanssa erittäin lujia typpiteräksiä, jotka ovat lähes tasoissa standardien keraamisten materiaalien kanssa. Näitä uudentyyppisiä teräksiä voidaan soveltaa rakenteellisiin elementteihin, mutta ne voivat saavuttaa vielä suuremmat painosäästöt, jos niitä käytetään suunnittelun alkuvaiheessa. Mitä tulee lujiin kuituihin, esimerkiksi IBD C1 HT -vuoraukseen, niillä on ominaisuudet, jotka ovat lähes 20% korkeammat kuin tavallinen vuori, mutta jopa 10% korkeammat kuin muilla IBD-vuorauksilla; niiden parametrien heikkeneminen lämpötilan noustessa on myös hitaampaa, mikä on erityisen tärkeää nykyaikaisten taistelukenttien äärilämpötilojen vuoksi. Äskettäin kehitetyissä koneissa käytettävien nanomittakaavaisten terästen ja nanokeramiikan lisäksi IBD on kehittänyt myös uusia komposiittimateriaaliratkaisuja, jotka mahdollistavat monimutkaisten kaarevien geometristen elementtien tuottamisen, mikä mahdollistaa 100% kattavuuden suojatulla alueella lähes ilman ballistisia aukkoja. Tätä ratkaisua käytetään erityisesti pohjaelementtien valmistuksessa, missä pienin rako voi vaarantaa koko suojan.
IBD on myös onnistunut kehittämään nanokomposiittilaminaatteja, joiden lujuus on kasvanut niin merkittävästi, että ne voivat korvata koneen rakenneosia ja toimia samalla korkeatasoisena ballistisena suojana. Alhaisen pintatiheytensä vuoksi tämän suojaustason kokonaispaino pienenee merkittävästi. Nämä komposiitit perustuvat edellä mainittuihin IBD: n nanoteknologiamateriaaleihin. Erityisiä liimausprosesseja on kehitetty ja niistä valmistetaan rakenteellisista materiaaleista valmistettuja nanokomposiittilaminaatteja, jotka tunnetaan nimellä IBD FlexiComp ja joilla on parempi rakenteellinen lujuus ja ballistinen suorituskyky. Koska niiden tiheys on 10% pienempi kuin tavallisissa laminaateissa, näiden materiaalien elastiset ominaisuudet ovat kaksi kertaa korkeammat. Tämän suuren lujuuden ansiosta ne voidaan integroida koneen suunnitteluun, kun taas ballistiset ominaisuudet mahdollistavat sen selviytymisen korkean tason uhista, kun taas FlexiComp-materiaaleilla on hyvät mahdollisuudet painonpudotukseen. Niiden käyttö voidaan toteuttaa kahdessa eri lähestymistavassa. Suora lähestymistapa on käyttää niitä suojana miinoja ja IED -laitteita vastaan lisävarusteena pyöräkoteloissa, lokasuojissa, miinolaattoina ja erillisissä sisälattioissa. Volumetrisiä osia muovaamalla ne voivat korvata muita ratkaisuja, kuten hitsaamalla tai ruuvaamalla koottuja kokoonpanoja. Toinen lähestymistapa on komposiittiosien, kuten luukkujen, moottoriluukkujen, peräovien ja luiskien, integrointi. Ne muodostavat suuren osan ajoneuvon kokonaispinnasta, ja siksi absoluuttinen painonpudotus on erittäin merkittävä. STANAG 4569, taso 4, tämä painonpudotus on 1500 kg 8x8 -koneella (katso taulukko). Valmistuskustannusten osalta IBD: n kehittämät prosessit mahdollistavat komposiittiosien valmistamisen ilman autoklaaveja, mikä tarjoaa merkittäviä kustannussäästöjä erityisesti suurille komponenteille.
Näitä komponentteja valmistaa tällä hetkellä Rheinmetall Chempro, jonka tehtävänä on hallita IBD Deisenroth Engineering -teknologioita, kehittää ne tuotantoprosessiksi kilpailukykyisten hintojen saavuttamiseksi, kehittää edelleen erikoisratkaisuja ja seurata niitä koneen hyväksymisprosessiin saakka. Uusimpien kehittyneiden tekniikoiden avulla valmistettujen komponenttien toimitukset alkoivat vuoden 2013 alussa, pääasiassa KMW-Rheinmetallin AMPV-koneita ja Iveco DV-KMW: n keskikokoista ajoneuvoa. Yli tusina alkuperäislaitteiden valmistajia ympäri maailmaa saa pian komponentteja, joiden avulla he voivat todella vähentää koneidensa painoa, mikä lisää hyötykuormaa ja alentaa elinkaarikustannuksia, Rheinmetallin suojaosasto sanoi.
Rheinmetall Chempron passiivivalikoima sisältää erilaisia versioita Amap (Advanced Modular Armor Protection) -perheestä. Tämä perhe käyttää uusinta IBD: n kehittämää tekniikkaa. Amap -tuotteet yhdistetään tyypillisesti tarjoamaan haluttu suoja monenlaisia uhkia vastaan. Erilaisten läpinäkymättömien tuotteiden joukossa on Amap-B-ballistinen ratkaisu, joka suojaa pienaseita ja keskikokoisia ammuksia vastaan, Amap-M-miinasuojaus, Amap-IED, joka on suunniteltu torjumaan IED: tä, Amap-L-vuoraukset, jotka suojaavat taistelutilaa absorboimalla toissijaisia sirpaleita, Amap-SC: tä HEAT-ammuksia vastaan ja lopuksi Amap-X-ratkaisua, joka suojaa kaupunkiolosuhteille tyypillisiltä uhilta.
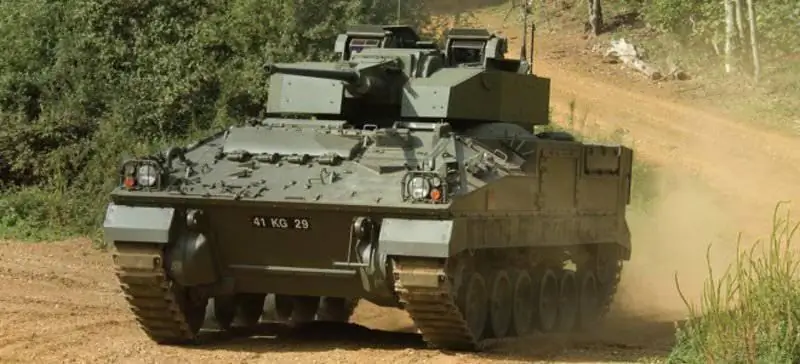
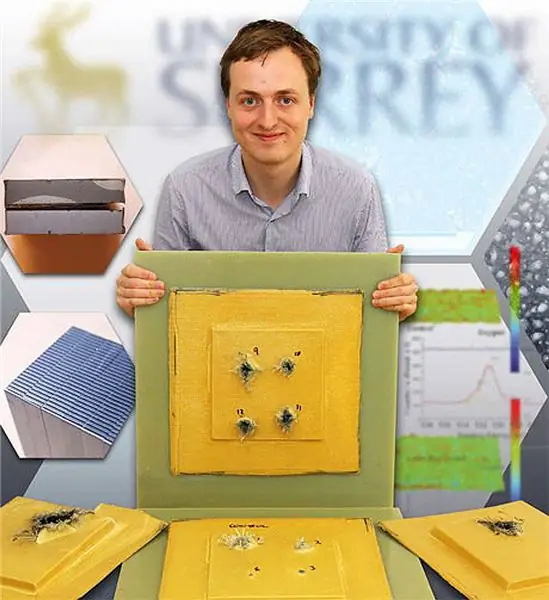
Lockheed Martin UK: n ja Surreyn yliopiston kehittämä uusi liimaustekniikka voisi parantaa merkittävästi panssaroitujen ajoneuvojen, kuten Warrior BMP: n (yllä) suojaa
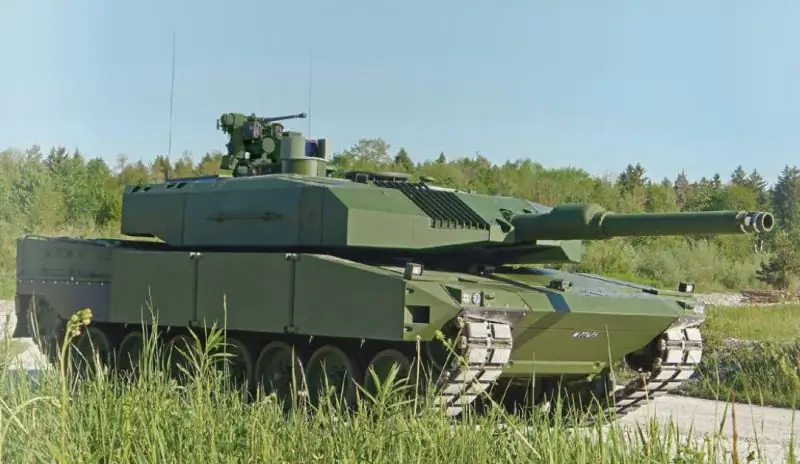
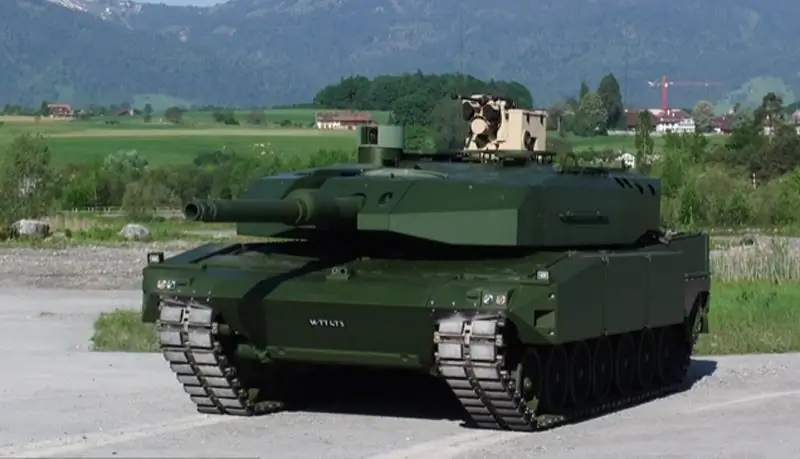
Muut SidePro-ATR-moduulit MBT Leopardille
On huomattava, että Rheinmetall -konsernissa toinen yritys harjoittaa passiivista suojaa, Rheinmetall Ballistic Protection GmbH, joka sai uuden nimensä 1. tammikuuta 2013. Aiemmin sitä kutsuttiin Rheinmetall Verseidag Ballistic Protection GmbH: ksi. Rheinmetallin kokonaan omistama yritys on erikoistunut panssariratkaisujen suunnitteluun ja valmistukseen kevyisiin sotilasajoneuvoihin, joissa käytetään materiaaleja, kuten keramiikkaa, kehittyneitä metalleja ja erikoiskankaita.
Vaikka Ruag Defence -valikoimassa on edelleen ratkaisuja dynaamiseen suojaukseen (aktiivinen reaktiivinen panssari), se ei enää näytä kuluttajien silmissä ultramodernina yrityksenä, joka kykenee parantamaan keskikokoisten ja raskaiden ajoneuvojen kestävyyttä. Tältä osin sveitsiläinen yritys kiinnitti huomionsa täydellisten passiivisten ratkaisujen kehittämiseen, jotka pystyvät selviytymään kineettisistä ja muotoilluista varauksista. SidePro-ATR-järjestelmä ylittää paljon RPG-7: n aggressiivisuuden, koska se pystyy käsittelemään symmetrisissä skenaarioissa käytettyjä muotoisia varauksia, kun taas perusversio takaa tason 5 ballistisen suojan. SidePro-ATR esitettiin ensimmäisen kerran yleisölle vuonna 2012, Tämä järjestelmä on skaalautuva, joten sitä voidaan käyttää sekä panssaroiduissa henkilöautoissa että tankeissa. Perusversiossa sen paksuus on 400 mm, ja sen massa on verrattavissa reaktiivisen liuoksen massaan (eli noin 300 kg / m2). Tämä järjestelmä on hyväksytty Leopard 2A4 -säiliöön. Ballistisen suojan tasoa voidaan nostaa merkittävästi siihen pisteeseen asti, että järjestelmä kestää 120 mm: n pitkänomaisen ytimen iskun, vaikka tältä osin ei toimitettu tietoja.
SidePro-ATR: n skaalautuvuus mahdollistaa sen käytön symmetrisissä ja epäsymmetrisissä taisteluskenaarioissa. Toinen ratkaisu kineettisten ampumatarvikkeiden ja IED: ien torjumiseksi nimellä SidePro-KE / IED testattiin Fennekin panssaroidulla tiedusteluautolla, joka on käytössä Saksan ja Alankomaiden kanssa. Pääasiassa keramiikkaan perustuva ratkaisu oli tarkoitettu torjumaan ensimmäisen sukupolven IED -laitteita. Uudet tienvarsipommit, joita käytetään eri teattereissa, tuottavat tuhansia nopeita sirpaleita, ja siksi tarvitaan erittäin hyviä monivaikutteisia ominaisuuksia. Siitä lähtien Ruag on kehittänyt KE / IED-järjestelmää siirtymällä pois keramiikasta ja käyttämällä laajentumattomia monikerroksisia pusseja. Uusi SidePro-KE / IED-ratkaisu, joka on ollut saatavilla vuodesta 2012 lähtien, tarjoaa tason 4 /5 suojan kineettisiä aseita vastaan ja sillä on erittäin korkea monivaikutteinen suorituskyky. Jos oletetaan, että runko on valmistettu 7 mm: n ballistisesta teräksestä, 30 mm: n paneeli voi tarjota täyden suojan, ja KE / IED -järjestelmä mahdollistaa pienimmän painonnousun vain ajoneuvotyypistä riippuen. Tämä ratkaisu odottaa useiden valmistajien kanssa.
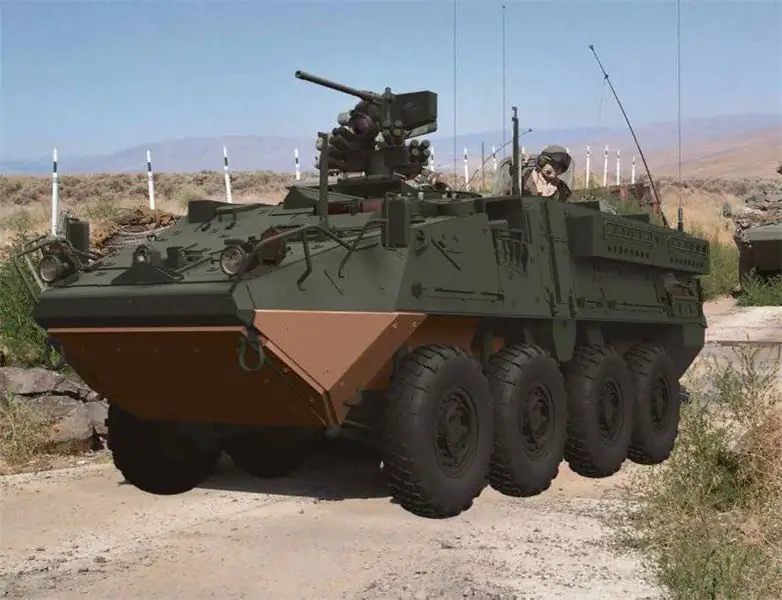
Ruag on viimeistellyt SidePro KE / IED -laitteen. Kuvayhdistelmä esittää järjestelmän elementtejä, jotka on suunniteltu torjumaan uusia laitteita, jotka tuottavat useita fragmentteja.
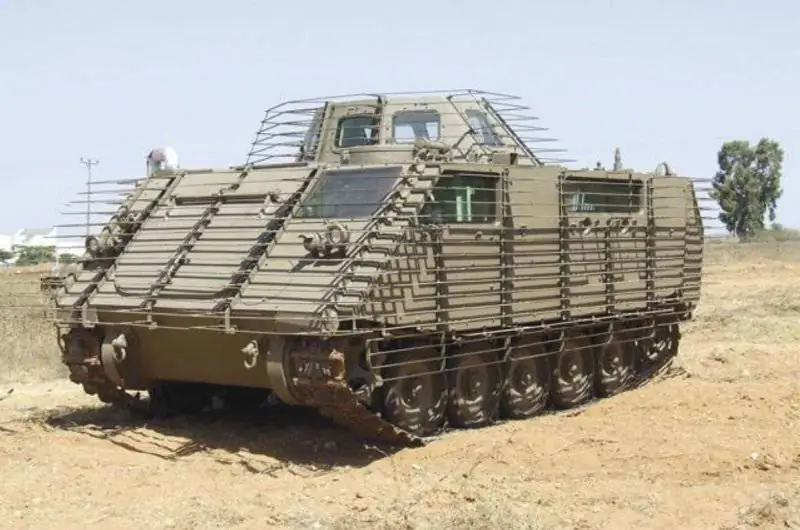
BTR M113, joka on varustettu passiivisella RPG-vastaisella rauta-seinällä Israel Military Industries, yhdistää passiivisen ja ristikkopanssarin.
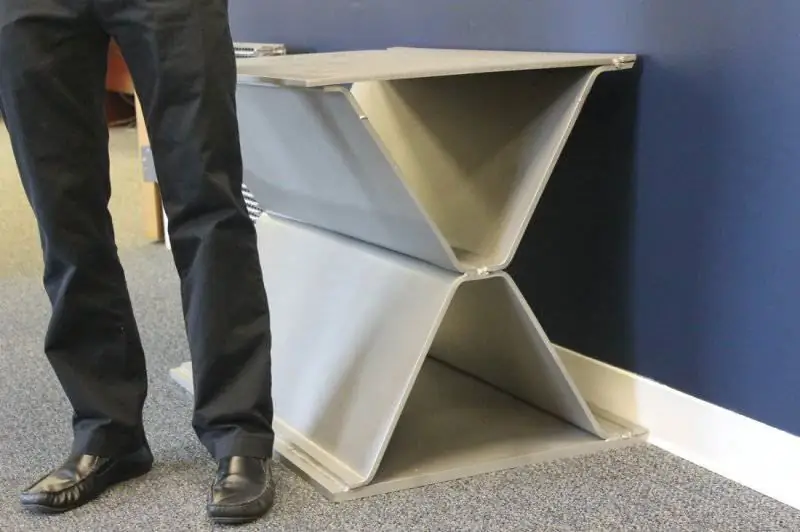
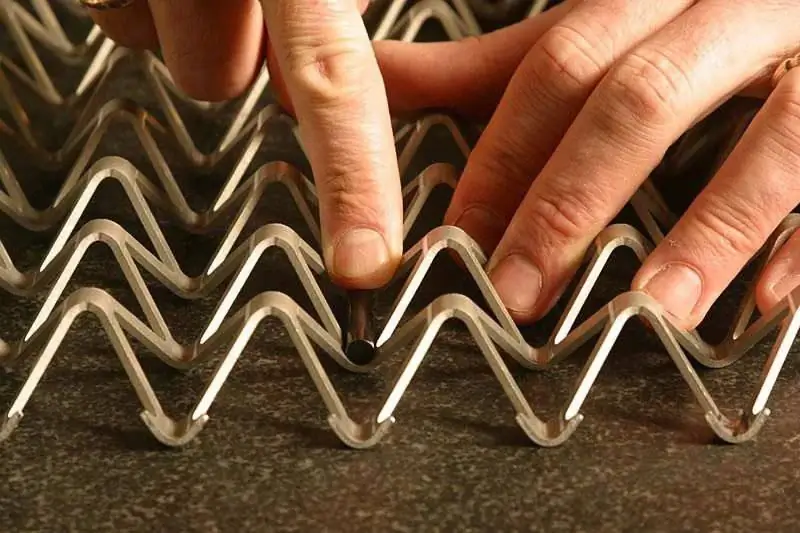
Ceradyne ja Cellular Materials International ovat kehittäneet pohjalevyn, joka perustuu CMI MicroTruss -alumiinikennoon, joka imee jopa kolmanneksen räjähdyksen tuottamasta energiasta. Alla on lähikuva MicroTruss-materiaalista.
Esimerkki painonpudotuksesta 8 x 8 koneelle, jossa on IBD FLEXICOMP -komponentteja
Paino kg
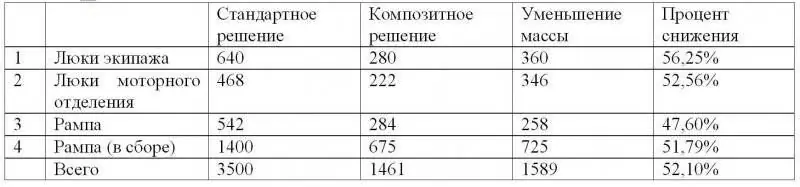
Plasan Sasa on edelleen yksi passiivisen varausalan avaintoimijoista. Tällä alalla ei anneta teknisiä yksityiskohtia, mutta yhtiö toimii aktiivisesti sekä lisävarauksissa että esivalmistetuissa rakennuksissa. Toinen lähestymistapa otettiin käyttöön kehittämällä Navistar MaxxPron Mrap ja Oshkoshin M-ATV. "Tämän ansiosta voimme lisätä tuotantoa käyttämällä työvoimaa ilman hitsaustaitoja, koska Lego-tyylinen lähestymistapamme perustuu lohkoihin, jotka sisältävät kaikki komponentit, jotka voidaan koota minimissaan", yrityksen lähde sanoi. Jotkut yrityksen yli kahdesta sadasta insinööristä kehittävät uusia ratkaisuja, jotka voivat johtua uusien materiaalien tai innovatiivisten geometristen ratkaisujen syntymisestä. Järjestelmälähestymistapa on edelleen suojausjakson ytimessä.
IMI on äskettäin kehittänyt joukon passiivisia ja reaktiivisia ratkaisuja uusimpien IED -tyyppien torjumiseksi, mukaan lukien erilaiset EFP- tai SFF (Self Formed Fragmentation) "iskusydämet" ja uusimmat RPG -mallit. Yhtiö on ehdottanut passiivista Iron Wall -ratkaisua, joka perustuu metallin ja komposiittien yhdistelmään, jota on täydennetty ristikkopanssarilla. Riippuen vaaditusta suojaustasosta paksuus voi vaihdella välillä 110-150 mm ja paino 200-230 kg / m2. Rauta -muuria käydään parhaillaan sotilaallisia kokeita Israelin armeijan kanssa.
IMI tarjoaa myös ristikkopanssarinsa itsenäisenä järjestelmänä. L -VAS (Light Vehicle Armor System - panssarointijärjestelmä kevyille ajoneuvoille) on suunniteltu suojaamaan ajoneuvoja, kuten panssaroituja henkilöautoja. Painon vähentämiseksi järjestelmä perustuu komposiittimateriaaleihin ja reaktiivisiin elementteihin, joista jälkimmäiset sisältävät vähintään energisiä materiaaleja. Tämä vähentää epäsuoria häviöitä ja materiaalityyppi välttää vierekkäisten elementtien toissijaisen räjähdysvaaran. IMI: n mukaan L-VAS-järjestelmä suojaa myös 14,5 mm: n panssarilävistyksiltä ja tykistön palasilta. Järjestelmä on täysin pätevä Israelissa M113 APC: lle ja sen ominaispaino on noin 200 kg / m2.
Saatavana on myös raskaampi aallonmurtajajärjestelmä. Tämä metalli- ja komposiittielementtejä sisältävä reaktiivinen panssari on suunniteltu torjumaan kolmea pääuhaa: RPG, SFF ja EFP. IMI on tehnyt laajoja testejä ja jatkaa parhaillaan pätevyyttä aloittaakseen ratkaisun, jonka paksuus on 350-400 mm ja paino 430-450 kg / m2 vuoden 2013 lopussa.
Ceradyne on toinen merkittävä toimija passiivisessa varauksessa. Ceradynen presidentin Mark Kingin mukaan teräs on edelleen varausliiketoiminnan päämateriaali, jonka tavoitteena on parantaa suorituskykyä ja vähentää kustannuksia. "Yhdysvalloissa ratkaiseva tekijä on pääasiassa ajoneuvon hankintakustannukset, ei sen käyttöikä, ja tämä toimii päivityksiä vastaan", King sanoi AUSA -konferenssissa vuonna 2012. Yhdysvalloissa korostettiin määrä, mikä toi eurooppalaiset suojajärjestelmien kehittäjät Yhdysvaltojen edellä. King korosti kuitenkin, että Amerikka edistyy parhaillaan ja keskittyy lähinnä räjähdysvaaralliseen rungon suojaan, koska ballistista suojaa pidetään ratkaistuna ongelmana. King arvioi myönteisesti Yhdysvaltojen armeijan kiinnostuksen ratkaista ongelman, joka koskee esimerkiksi Humveen (20 miljoonaa dollaria kehittämiseen) ajoneuvojen pohjan suojaamista. Ceradyne on yksi niistä, jotka kilpailevat ehdottomasti modernisointisopimuksesta. Vaatimus tarjoaa maksimaalisen suojan ja merkittäviä painosäästöjä, jotta voidaan vähentää vaikutusta koneen suorituskykyyn.
Ceradyne on kehittänyt MicroTruss -ratkaisun Cellular Materials International Inc: ltä (CMI). Tämän huokoisen alumiiniseosmateriaalin tiheys on 58 kg / m2 verrattuna vastaavan monoliittisen metalliliuoksen tiheyteen 112 kg / m2. Tämä ratkaisu eroaa rungon "V" -kulmasta vain 5 °, mikä riittää heijastamaan räjähdysaaltoa ja jonka massa on 300 kg. MicroTruss takaa jopa 30% räjähdysenergian absorboitumisen, mikä ei ainoastaan rajoita miehistön kapseliin kohdistuvaa iskua, vaan myös vähentää ajoneuvon pystysuoraa liikettä. Ceradyne on myös vahvasti mukana Flyer Gen.2 -varausohjelmassa, joka on suunnattu GMV 1.1: n Special Operations Forces -hankkeeseen. Yhtiö on kehittänyt sarjan, joka tarjoaa B6 (.357 Magnum) -tason ballistisen suojan oville ja katto.
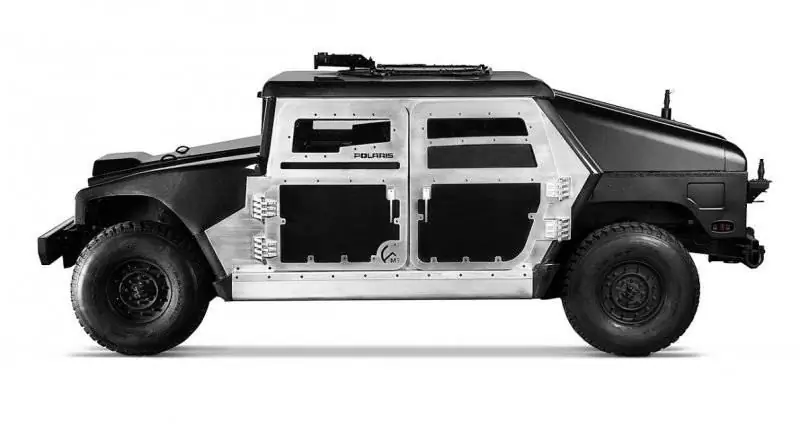
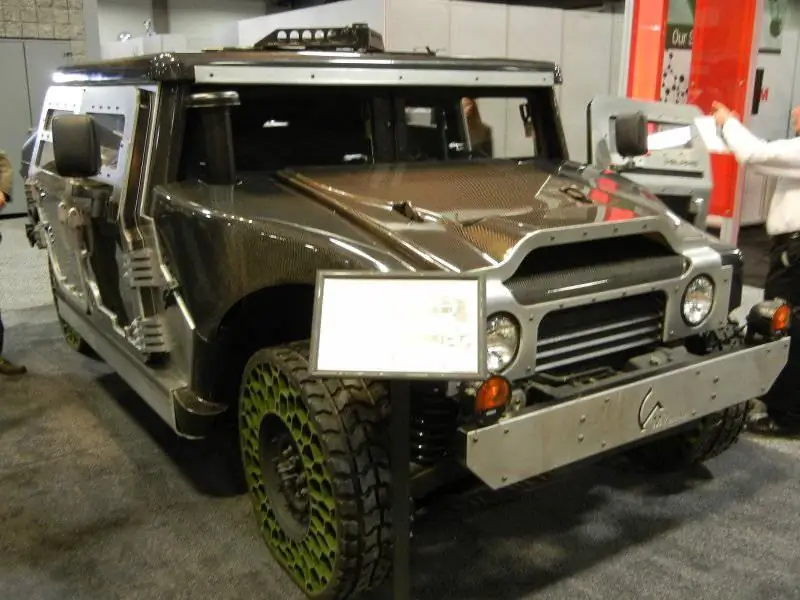
Polaris Defense ja M9 Defense Armor Technology ovat kehittäneet hybriditeräskomposiittirakenteisen panssarin, joka voi vähentää merkittävästi Humveen omaa painoa säilyttäen samalla suojaustason. Oikealla kuvassa olevan prototyypin omapaino on vain 3400 kg, mikä on lähes 50% vähemmän kuin tason 3 suojalla varustetussa Humveessa.(Huomaa auton pyörät alhaalla)
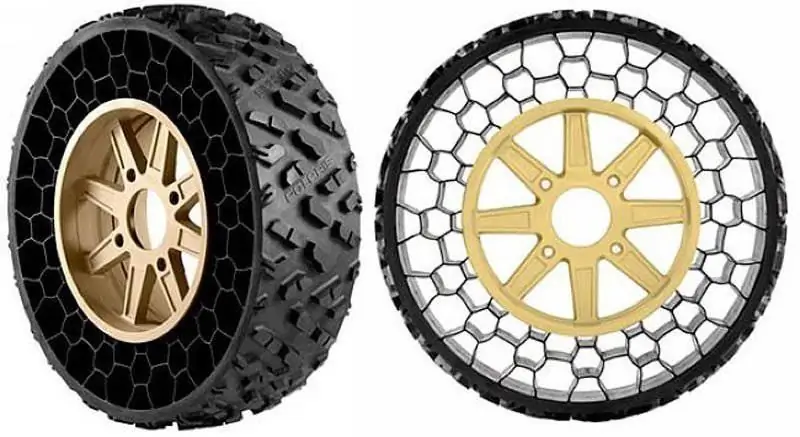
Suojaus koskee myös sitä, että taistelukentälle ei jätetä, jos rengas puhkeaa. Polaris Defence -laitteiden ei-pneumaattiset pyörät takaavat huomattavasti paremman kestävyyden verrattuna vakiorenkaisiin ja kestävät 12,7 mm: n luodin. Tällä hetkellä niitä on saatavana paitsi autoihin, myös Hummer -luokkaan, mutta nyt näitä vanteita kehitetään myös raskaampiin Mraps -luokan autoihin.
Ceradyne osallistuu myös Marines Personnel Carrier -ohjelmaan yhteistyössä Lockheed Martinin ja Patrian kanssa suomalaiseen Patria AMV -malliin perustuvalla Marine Corps -autolla. On syytä huomata, että 28. marraskuuta 2012 ilmoitettiin, että 3M Group osti Ceradynen, minkä ansiosta se voi investoida enemmän T & K -toimintaan ja innovatiivisiin ratkaisuihin.
Suunnittelun ja suojauksen yhdistäminen on haluttu ratkaisu kevyisiin ajoneuvoihin. AUSA 2012 -tapahtumassa Polaris Defense esitteli prototyyppisen Humvee -ajoneuvon, jossa oli uusi konsepti, jonka se kehitti yhteistyössä M9 Defencein kanssa. Haasteena on vähentää omapainoa säilyttäen ja lisäämällä suojaustasoa. Tätä varten Polaris-M9-tiimi poisti kaikki yläpanssarit tarkastellakseen rakenteellisia panssarikonsepteja. Sitten kaikki poistettiin autosta, vain paljas alusta jätettiin, ja sitten siihen asetettiin kevyt hybridi (teräs-komposiittimateriaali) rakenne. Tämä rakenteellinen panssari voi tarjota tason 3 suojan, jonka paino on 70 kg / m2 ja jonka paino on 83 kg / m2, ja se kestää 12,7 x 99 mm: n luodin, vaikka Polaris-M9-ryhmä on varma, että ne voivat saavuttaa taso 3+ (12, 7 mm panssarilävistysluoti). Polaris-M9-ratkaisu suojaa myös moottoria. Vaikka vakio Hummer -panssaroitu ajoneuvo painaa noin 6350 kg, ehdotetun ratkaisun ansiosta sen paino voidaan alentaa 3400 kg: aan. Hybridirakenteisessa panssarissa käytetään ei-eksoottista materiaalia, minkä ansiosta Polaris-M9-tiimi voi puhua uuden ratkaisun hinnasta, joka on verrattavissa nykyisten ratkaisujen hintaan. Lisäksi tämä materiaali on valettu monimutkaisiin muotoihin, mikä johtaa muun muassa saumattomiin V-muotoisiin pohjaan. Haluttu muoto saavutetaan hydraulimuovauksella - nopea prosessi, joka auttaa vähentämään kustannuksia. Polaris-M9-tiimin mukaan tämä tekniikka voi vähentää painoa 40 prosenttia.
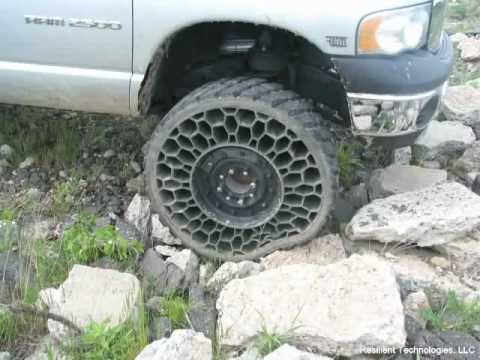
Polaris Defence ei-pneumaattisten pyörien esittely
Puolustusyhtälö sisältää toisen termin, joka liittyy suoraan liikkuvuuteen - pyörä. Joustavan teknologian hankinnan jälkeen Polaris Defense tarjoaa nyt ei-pneumaattisia renkaita (NPT). Pyörien kulutus on yksi turbiinimoottorin tärkeimmistä logistisista ongelmista, ja ydinsulkusopimus auttaa monissa tapauksissa ratkaisemaan sen. Afganistanin erikoisoperaatiojoukkojen komennon mukaan tavanomaiset renkaat kulkevat noin 1300 km, kun taas 12,7 mm: n luodin lävistämä NPT -pyörä voi matkustaa yli 8 000 km ja syrjäyttää siten varapyörät toimitusketjusta samalla kun parannetaan ajon laatua. NPT -prototyyppejä on jo tehty Hummer -ajoneuvoille. Nykyinen tavoite on joukko NPT -renkaita 7,7 tonnin koneelle, mikä on lähes JLTV General Purpose -vaihtoehdon kokonaispaino. Yritysten edustajien mukaan mallinnus osoitti, että massa voi nousta 18 tonniin, toisin sanoen pyörät kestävät Mrap -luokan auton. Hyötykuorman kasvaessa tekniikka pysyy samana, ja yrityksen simulointiohjelmat mahdollistavat erittäin tarkat ennusteet. Se, mikä muuttuu, on materiaali, jonka on sopeuduttava massaan, joka puolestaan ei ole vielä ilmestynyt tulevaisuudessa.