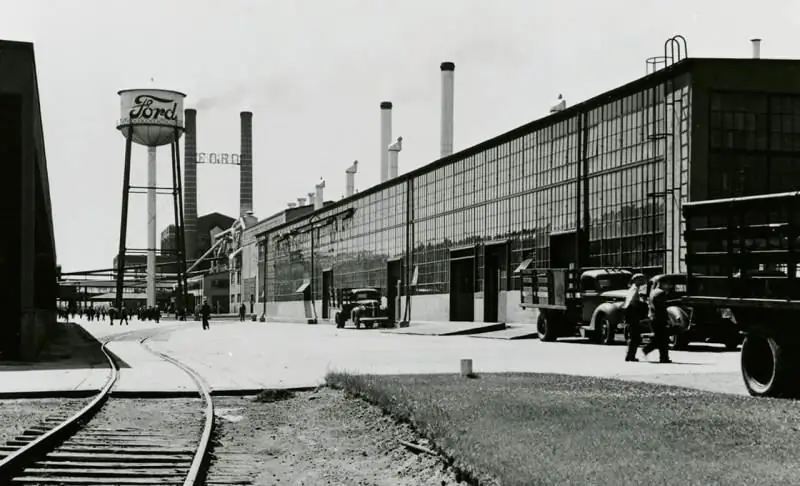
Strategiset tekniikat
Ennen kuin tutustutaan panssaroidun tuotannon ominaisuuksiin Michigan Fordin tehtaalla Detroitissa (USA), kannattaa lyhyesti selittää olosuhteet, joissa panssaroitu teollisuus perustettiin Neuvostoliitossa. Kuten tiedät, kaikki opitaan vertaamalla.
Panssarituotanto toisen maailmansodan aikana oli yksi tärkeimmistä strategisen edun tekijöistä. Sodan alkaessa Neuvostoliitto joutui tuhoisaan asemaan - kaikki panssaroitu tuotanto keskittyi maan eurooppalaiseen osaan. Saksan armeijan nopea eteneminen voi halvauttaa kokonaan panssaripanssarin tuotannon maassa. Vain uskomattomien ponnistelujen kustannuksella evakuoida osa tehtaista itään sodan alussa oli mahdollista palauttaa panssarituotanto. Tärkeimmät "panssaritehtaat" olivat Kuznetsk, Nizhny Tagil ja Magnitogorsk metallurgiset tehtaat.
Asia ei kuitenkaan rajoittunut yksinkertaiseen tuotannon siirtämiseen uuteen paikkaan etulinjan takana. Suurin osa uusista tehtaista ei ollut sopeutettu panssaripanssaroiden sulatukseen - ennen sotaa tehtaat työskentelivät rautametallurgia -kansakomissaarin tarpeisiin. Wartime on lisännyt omia säätöjään. Nyt avotakka-uuneissa oli usein heikosti koulutettuja työntekijöitä, ja akuutti ongelma oli erityisten lämpö-, puristus- ja metallityökalujen puute. Siksi panssarituotannon siirtoon liittyi sotilaallisen teräksen sulatustekniikan vakava rakenneuudistus. Niinpä oli tarpeen mukauttaa tuotanto 120-180 tonnin suuriin avotakka-uuneihin, lukuun ottamatta diffuusiohapetuksen prosessia. Panssarilevyjen ja panssariosien kovettaminen piti suorittaa vedessä.
Tällainen yksinkertaistaminen ei voinut vaikuttaa vastaanotetun panssarin laatuun. Tämä pätee erityisesti vaikeimmin valmistettavan erittäin kovan säiliöteräksen 8C valmistukseen. Ensimmäiset panssarilevyjen näytteet testissä osoittivat murtuman merkittävää liuskekiveä ja kerrostumista, suurta taipumusta halkeamien muodostumiseen hitsauksen ja suoristuksen aikana. Tämän lisäksi kenttäkokeet paljastivat panssarinäytteiden liiallisen haurauden kuoripalon aikana.
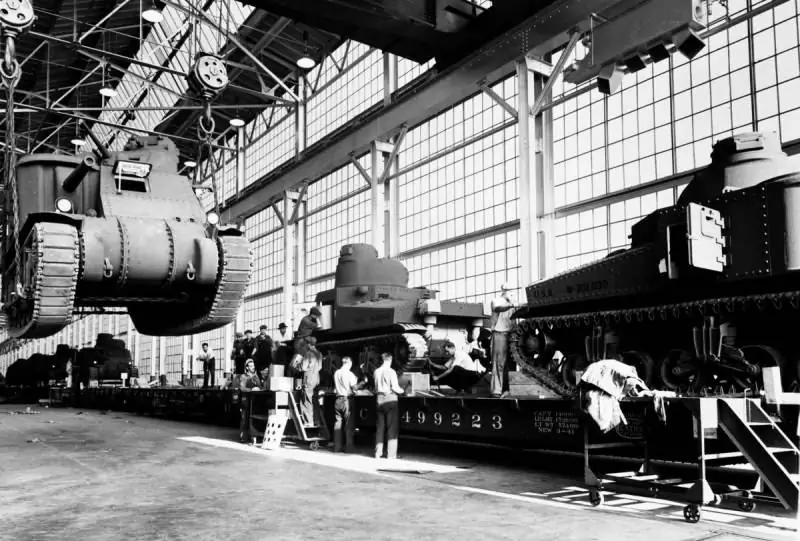
Tällaisia vikoja ei voitu jättää huomiotta. Ja erikoistuneessa TsNII-48: ssa he ovat kehittäneet useita parannuksia. Ensinnäkin panssariterästä oli tarkoitus sulattaa tästä lähtien vain esilämmitetyissä uuneissa "siviili" -terästen sulattamisen jälkeen. Teräksen piti kiehua avotakka-sulatushauteessa vähintään puolitoista tuntia ja kaataa neliömäisiin tai kuperamuotteihin. Lisäksi metallurgit kiinnittivät erityistä huomiota alkuperäisen valuraudan rikkipitoisuuteen (enintään 0,06%) sekä hiileen ja mangaaniin. Yhdessä muiden toimenpiteiden kanssa tämä mahdollisti panssarin laadun parantamisen. Erityisesti halkeaman liuskekiven ja kerrostumisen vähentämiseksi.
Tärkeä ongelma oli kotitalouksien panssarin lämpökäsittelytekniikka. Yksinkertaisesti sanottuna panssarilevyjen kovettuminen ja karkaisu veivät liikaa aikaa ja energiaa, ja tarvittavat laitteet puuttuivat. Oli tarpeen yksinkertaistaa prosessia. Tältä osin annamme tyypillisen esimerkin. Vuonna 1942 TsNII-48: n metallurgit onnistuivat yksinkertaistamaan lämpökäsittelyprosessia niin paljon, että vain osissa KV- ja T-34-säiliöiden pohjoja he säästävät noin 3230 uunituntia 100 runkoa kohden.
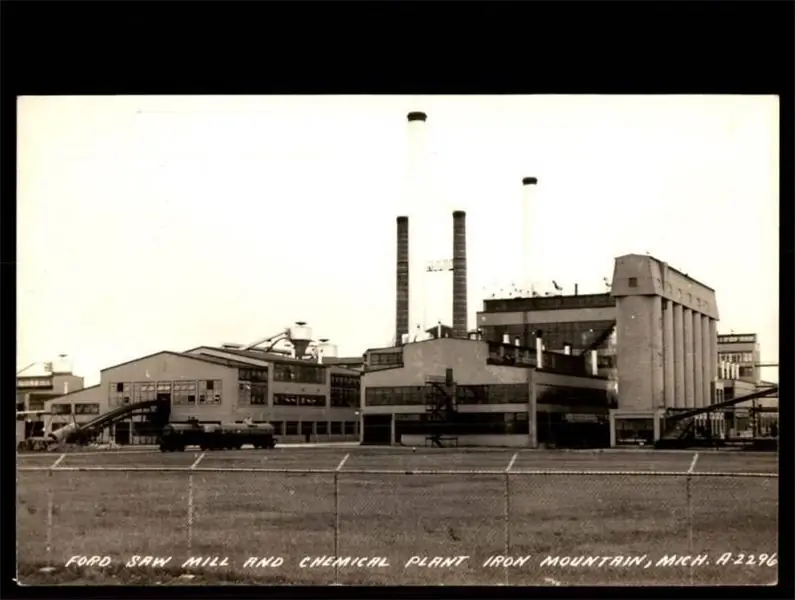
Siitä huolimatta Neuvostoliiton sodan loppuun asti olosuhteet strategisesti tärkeiden panssaripanssarien tuottamiselle olivat kaukana vaadituista. Samaa ei voida sanoa merentakaisen kumppanin sotateollisuudesta, jonka alueelle maailmansota ei vaikuttanut. Neuvostoliiton metallurgisten insinöörien oli varmistettava tämä jälleen 26. helmikuuta 1945, 72 päivää ennen voittoa.
Amerikkalaista luksusta
Venäjän tiedeakatemian Uralin haaratoimiston historian ja arkeologian instituutin historiatieteiden kandidaatti Vasily Vladimirovich Zapariy ilmoitti Neuvostoliiton valtuuskunnan vierailun vähän tunnetusta vierailusta Fordin panssaritehtaalla Detroitissa. Tiedemiehen materiaali perustuu Venäjän valtionarkistoon (RGAE) tallennettuun neuvostoliiton metallurgien raporttiin Yhdysvaltojen -matkan tuloksista. On huomattava, että RGAE on vain suuren isänmaallisen sodan aikakauden arkistodokumenttien aarrearkku, joka liittyy sotilastarvikkeiden ja varusteiden tuotantoon. Jää vain arvailla, kuinka paljon salaisuuksia arkisto pitää toistaiseksi salassa pidetyssä todisteessa.
Detroitista palanneiden insinöörien mukaan Fordin tehtaan panssaroitu työpaja oli rakennus, joka koostui kahdesta jännevälistä, joiden pituus oli 273 metriä, leveys 30 metriä ja korkeus noin 10 metriä. Samaan aikaan kauppa ei haissut haarniskoja. Se oli tarkoitettu pääasiassa teräksen lämpökäsittelyyn ja leikkaamiseen. Tämä luonnollisesti herätti erityistä kiinnostusta Neuvostoliiton metallurgien keskuudessa, kun otetaan huomioon edellä kuvatut kotimaisen panssaroidun tuotannon ongelmat. Ford Motors -korjaamon tärkein tuotantoprofiili oli jopa 76 mm paksut panssarit. Lämpökäsiteltyjä teräslevyjä käytettiin kevyiden ja keskipanssaroitujen ajoneuvojen runkojen hitsaamiseen muissa Detroitin tehtaissa.
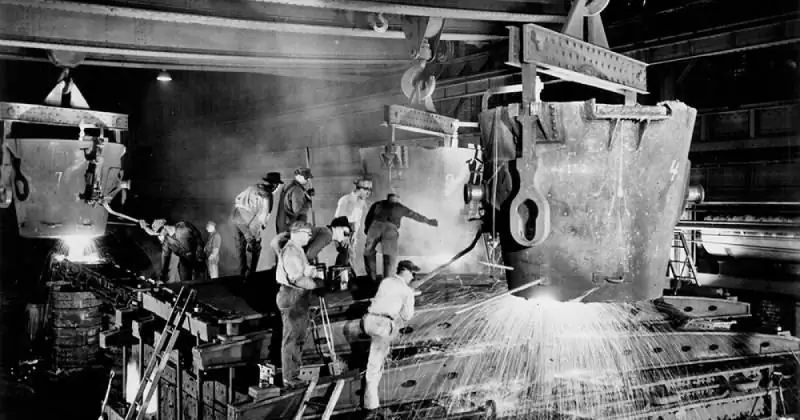
Ensinnäkin tuotantoprosessin koneistus teki vaikutuksen Fordin työpajoihin. Sulamisen ja rullaamisen jälkeen panssarilevyt toimitettiin lämpökäsittelylaitokselle hydraulipöytäkuormaajilla United. Kuormaajat puolestaan ottivat panssarin työpajan lähellä sijaitsevilta rautatielautoilta. Itse työpajassa oli kaksi sillanosturia, jotka on suunniteltu siirtämään panssarilevyjä kaikkien teknisten toimintojen aikana, karkaisuprosesseja lukuun ottamatta.
Panssarin tarvittavan kiteisen rakenteen luomiseksi käytettiin kahta puristinta, joiden kumpikin vaiva oli 2500 tonnia, viisi 70-metristä kuljettimen menetelmäuunia ja viisi 100-metristä kaasukarkaisukuljettimen uunia. Vettä syötettiin panssarin kovettumispuristimiin kuuden pumpun avulla kerralla, pumppaamalla yli 3700 litraa minuutissa. Kuten venäläiset insinöörit kirjoittivat, tällaisten puristimien suunnittelun monimutkaisuus ja kustannukset, jotka pystyvät samanaikaisesti leimaamaan ja jäähdyttämään punaisen kuuman haarniskan, olivat kohtuuttomia. Samaan aikaan oli epäilyksiä siitä, onko tarkoituksenmukaista käyttää puristimia panssariin, jonka paksuus on 30-76 mm. Tässä esille tuli jäähdytysveden voimakkuus.
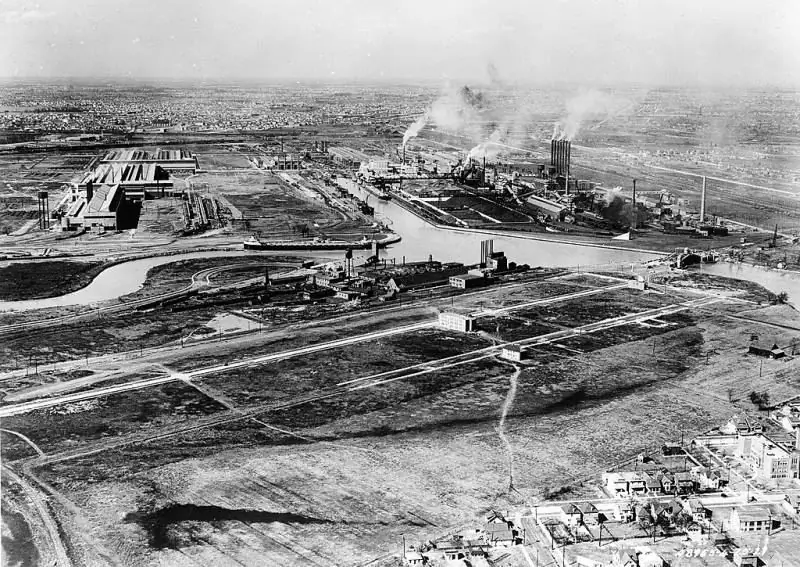
2500 tonnin puristimet eivät olleet ainoita Fordin panssariajoneuvossa. Toledon puristimet # 206 leikkasivat ohutta panssaria ja kehittivät 161 tonnin paineen. Panssaroissa, joiden paksuus oli yli 2,5 cm, käytettiin yksinomaan tulenleikkausta.
Vierailun aikana yrityksessä metallurgit pystyivät tarttumaan ohuen luodinkestävän panssarin kovettamiseen. Se pysyi 1000 tonnin puristimen alla 15 sekuntia, ja sitten arkki lähetettiin 2,5 tunniksi sammutukseen 900 celsiusasteessa ja neljän tunnin lomalle 593 asteessa.
Neuvostoliiton insinöörit havaitsivat kaiken tämän teknisen vaurauden, lukuun ottamatta erilaisia "pieniä lisävarusteita": hitsauskoneita, jyrsinkoneita, saksia ja vastaavia.
Panssarin lämpökäsittelyn pääpiirre oli jatkuva tuotannon virtaus. Lähes kaikissa käsittelyvaiheissa teräslevyt siirtyivät rulla- ja ketjukuljettimilla. Kuljetinta hallittiin keskikonsolista. Yhdessä viimeisistä vaiheista kaikki panssarilevyt tarkastettiin Brinell -kovuuden suhteen. Tässä tapauksessa testiparametrin vaihtelun arkin välillä tulee olla minimaalinen - enintään 0,2 mm.
Neuvostoliiton valtuuskuntaa kiinnosti erityisesti kaksi räjäytyspuhalluskonetta, jotka puhdistivat panssarilevyt lähes jokaisen teknisen toimenpiteen jälkeen. Tällaisen perfektionismin ja tällaisen ylellisyyden saivat vain amerikkalaiset, kaukana sota -ajan vaikeuksista.