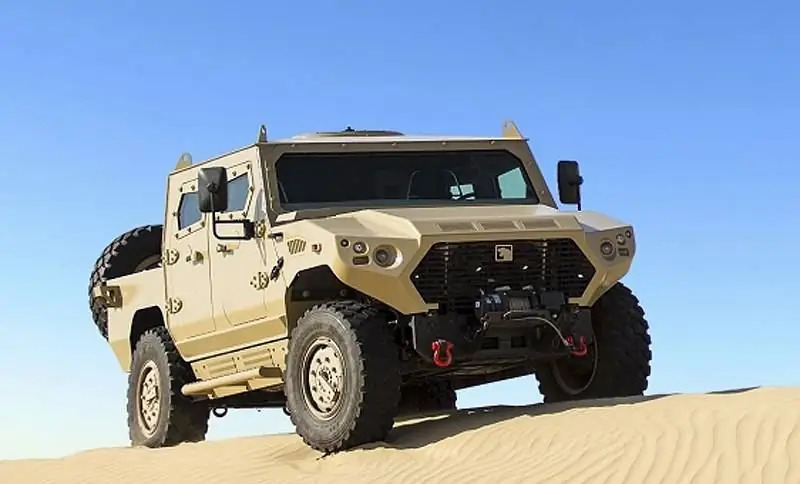
Panssari on miljoonia vuosia ihmiskuntaa vanhempi, ja se kehitettiin ensisijaisesti suojaamaan leuilta ja kynsiltä. On mahdollista, että krokotiilit ja kilpikonnat voivat osittain innostaa ihmisiä luomaan suojaavia elementtejä. Kaikki kineettisen energian aseet, olipa se esihistoriallinen maila tai panssaria lävistävä ammus, on suunniteltu keskittämään suuria voimia pienelle alueelle, ja sen tehtävänä on tunkeutua kohteeseen ja aiheuttaa sille mahdollisimman suurta vahinkoa. Näin ollen panssarin tehtävänä on estää tämä ohjaamalla tai tuhoamalla hyökkäysvälineet ja / tai hajauttamalla iskuenergia mahdollisimman suurelle alueelle, jotta minimoidaan mahdolliset vauriot työvoimalle, kuljetusjärjestelmille ja rakenteille, joita se suojaa.
Moderni panssari koostuu tyypillisesti kovasta ulkokerroksesta ammuksen pysäyttämiseksi, ohjaamiseksi tai tuhoamiseksi, välikerroksesta, jolla on erittäin korkea”murtumistyö”, ja viskoosisesta sisäkerroksesta halkeamien ja roskien estämiseksi.
Teräs
Teräksestä, josta tuli ensimmäinen panssaroitujen ajoneuvojen valmistuksessa laajalti käytetty materiaali, on edelleen kysyntää huolimatta panssaroiden syntymisestä, jotka perustuvat kevyisiin alumiini- ja titaaniseoksiin, keramiikkaan, polymeerimatriisin komposiitteihin, vahvistettu lasikuiduilla, aramidilla ja erittäin korkean molekyylipainon omaavaa polyeteeniä sekä komposiittimateriaaleja, joissa on metallimatriisi.
Monet terästehtaat, mukaan lukien SSAB, kehittävät edelleen erittäin lujia teräksiä erilaisiin painokriittisiin sovelluksiin, kuten lisävaippaan. Panssaroitu teräslaatu ARM OX 600T, saatavana 4-20 mm: n paksuisina, on saatavana taatulla kovuudella 570-640 HBW-yksikköä (lyhenne sanoista Hardness, Brinell, Wolfram; testi, jossa puristetaan vakioläpimittainen volframipallo materiaalinäytteeseen, jolla on tunnettu voima, mitataan muodostetun syvennyksen halkaisija; sitten nämä parametrit korvataan kaavalla, jonka avulla voit saada kovuusyksiköiden määrän).
SSAB korostaa myös, että on tärkeää saavuttaa oikea kovuuden ja sitkeyden tasapaino tunkeutumisen ja halkeamisen estämiseksi. Kuten kaikki teräkset, ARMOX 600T koostuu raudasta, hiilestä ja useista muista seosaineista, kuten pii, mangaani, fosfori, rikki, kromi, nikkeli, molybdeeni ja boori.
Käytetyille valmistustekniikoille on rajoituksia, etenkin lämpötilan suhteen. Tätä terästä ei ole tarkoitettu lisälämpökäsittelyyn; SSAB ei voi taata sen ominaisuuksia, jos se kuumennetaan yli 170 ° C: een toimituksen jälkeen. Yritykset, jotka voivat kiertää tämänkaltaiset rajoitukset, saavat todennäköisesti panssaroitujen ajoneuvojen valmistajien tarkan tarkastelun.
Toinen ruotsalainen yritys, Deform, tarjoaa luodinkestäviä panssariteräksisiä kuumamuovattuja osia panssaroitujen ajoneuvojen valmistajille, erityisesti niille, jotka haluavat parantaa hyötyajoneuvojen / siviilikäyttöisten ajoneuvojen suojaa.
Yksiosaiset Deform-palomuurit on asennettu Nissan PATROL 4x4: een, Volkswagen T6 TRANSPORTER -bussiin ja Isuzu D-MAX -kuorma-autoon samasta materiaalista valmistetun kiinteän lattialevyn kanssa. Deformin kehittämä ja arkin valmistuksessa käytetty kuumamuovausprosessi pitää kovuuden 600HB [HBW].
Yhtiö väittää pystyvänsä palauttamaan kaikkien markkinoilla olevien panssariterästen ominaisuudet säilyttäen samalla rakenteellisesti määritellyn muodon, kun taas tuloksena olevat osat ovat paljon parempia kuin perinteiset hitsatut ja osittain päällekkäiset rakenteet. Deformin kehittämässä menetelmässä levyt sammutetaan ja karkaistaan kuuman taonnan jälkeen. Tämän prosessin ansiosta on mahdollista saada kolmiulotteisia muotoja, joita ei voida saada kylmämuovauksella ilman pakollista tällaisissa tapauksissa "hitsit, jotka rikkovat kriittisten pisteiden eheyttä".
Kuumamuovattuja teräslevyjä on käytetty BAE Systems BVS-10 ja CV90 -laitteissa ja 1990-luvun alusta lähtien monissa Kraus-Maffei Wegmann (KMW) -koneissa. Tilauksia on tulossa kolmiulotteisten panssarilevyjen valmistukseen LEOPARD 2 -säiliöön ja useita muotoiltuja levyjä BOXER- ja PUMA-ajoneuvoihin sekä useisiin Rheinmetall-ajoneuvoihin, mukaan lukien jälleen BOXER, sekä luukku WIESEL-ajoneuvoon. Deform toimii myös muiden suojaavien materiaalien kanssa, kuten alumiini, kevlar / aramidi ja titaani.
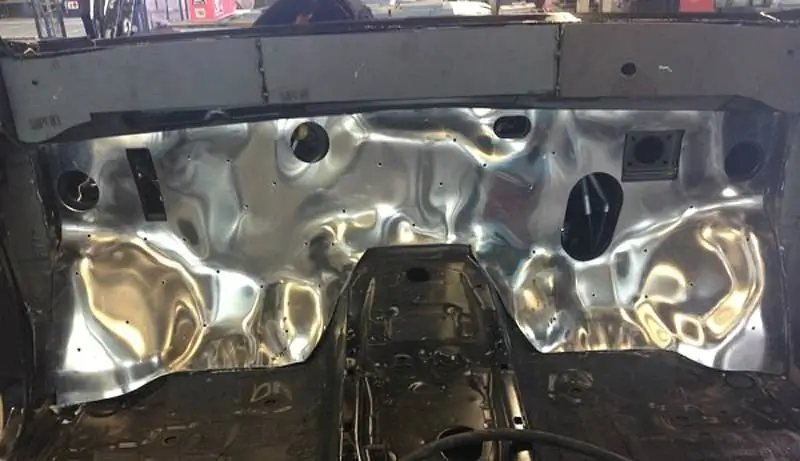
Alumiinin edistyminen
Panssaroitujen ajoneuvojen osalta alumiinipanssaria käytettiin ensimmäistä kertaa laajalti panssaroidun M113 -kuljettajan valmistuksessa, jota on valmistettu vuodesta 1960 lähtien. Se oli seos, nimetty 5083, joka sisälsi 4,5% magnesiumia ja paljon pienempiä määriä mangaania, rautaa, kuparia, hiiltä, sinkkiä, kromia, titaania ja muita. Vaikka 5083 säilyttää lujuutensa hyvin hitsauksen jälkeen, se ei ole lämpökäsiteltävä seos. Se ei kestä yhtä hyvin 7,62 mm: n panssaria lävistäviä luoteja, mutta kuten viralliset testit vahvistivat, se pysäyttää 14,5 mm: n Neuvostoliiton-tyyppiset panssaroivat luodit paremmin kuin teräs ja säästää samalla painoa ja lisää haluttua lujuutta. Tällä suojaustasolla alumiinilevy on paksumpaa ja 9 kertaa vahvempaa kuin teräs, jonka tiheys on pienempi 265 r / cm3, mikä vähentää rakenteen painoa.
Panssaroitujen ajoneuvojen valmistajat alkoivat pian pyytää kevyempiä, ballistisesti vahvempia, hitsattavia ja lämpökäsiteltäviä alumiinipanssaroita, mikä johti siihen, että Alcan kehitti 7039 ja myöhemmin 7017, joissa molemmissa oli enemmän sinkkiä.
Kuten teräs, leimaus ja myöhempi kokoonpano voivat vaikuttaa negatiivisesti alumiinin suojaominaisuuksiin. Hitsauksen aikana lämpövaikutteiset alueet pehmentyvät, mutta niiden lujuus palautuu osittain luonnollisen ikääntymisen aiheuttaman kovettumisen vuoksi. Metallin rakenne muuttuu kapeilla vyöhykkeillä lähellä hitsausta, mikä aiheuttaa suuria jäännösjännityksiä hitsaus- ja / tai asennusvirheiden sattuessa. Näin ollen valmistustekniikoiden pitäisi minimoida ne, mutta myös jännityskorroosion halkeamisen riski olisi minimoitava, varsinkin kun koneen käyttöiän odotetaan olevan yli kolme vuosikymmentä.
Jännityskorroosiokrakkaus on halkeamien syntyminen ja kasvu syövyttävässä ympäristössä, joka pyrkii heikkenemään seosaineiden lukumäärän kasvaessa. Halkeamien muodostuminen ja niiden myöhempi kasvu tapahtuu vedyn diffuusion seurauksena rakerajoja pitkin.
Halkeilulle alttiuden määrittäminen alkaa pienestä määrästä elektrolyyttiä poistamalla halkeamista ja analysoimalla se. Alhaisen venymän jännityskorroosiotestejä suoritetaan sen määrittämiseksi, kuinka pahasti tietty seos on vaurioitunut. Kahden näytteen mekaaninen venytys (toinen syövyttävässä ympäristössä ja toinen kuivassa ilmassa) tapahtuu, kunnes ne epäonnistuvat, ja sitten verrataan murtumiskohdan muovista muodonmuutosta - mitä enemmän näyte venyy vikaan, sitä parempi.
Jännityskorroosion halkeilua voidaan parantaa käsittelyn aikana. Esimerkiksi Total Materian mukaan, joka kutsuu itseään "maailman suurimmaksi materiaalitietokannaksi", Alcan on parantanut 7017: n suorituskykyä kiihdytetyissä jännityskorroosiokokeissa 40 kertaa. Saadut tulokset mahdollistavat myös korroosionestomenetelmien kehittämisen hitsattujen rakenteiden vyöhykkeille, joissa jäännösjännityksiä on vaikea välttää. Tutkimus metalliseosten parantamiseksi hitsausliitosten sähkökemiallisten ominaisuuksien optimoimiseksi on käynnissä. Uusien lämpökäsiteltävien seosten valmistuksessa keskitytään niiden lujuuden ja korroosionkestävyyden parantamiseen, kun taas ei -lämpökäsiteltyjen seosten työllä pyritään poistamaan hitsattavuusvaatimusten asettamat rajoitukset. Kehitettävät kovimmat materiaalit ovat 50% vahvempia kuin nykyisin käytössä olevat parhaat alumiinipanssarit.
Pienitiheyksiset seokset, kuten litiumalumiini, säästävät noin 10% painosta verrattuna aiempiin seoksiin, joilla on vastaava luodinkestävyys, vaikka ballistista suorituskykyä ei ole vielä arvioitu kokonaan Total Materian mukaan.
Myös hitsausmenetelmät, mukaan lukien robotit, paranevat. Ratkaistavia tehtäviä ovat muun muassa lämmönsyötön minimointi, vakaampi hitsauskaari energia- ja langansyöttöjärjestelmien parantamisen vuoksi sekä prosessin seuranta ja ohjaus asiantuntijajärjestelmien avulla.
MTL Advanced Materials kehitti yhteistyössä ALCOA Defence -yhtiön kanssa, joka on tunnettu alumiinipanssarilevyjen valmistaja, kehittääkseen yrityksen kuvaaman "luotettavan ja toistettavan kylmämuovausprosessin". Yhtiö toteaa, että panssarisovelluksiin kehitettyjä alumiiniseoksia ei ole suunniteltu kylmämuovaukseen, joten sen uuden prosessin pitäisi auttaa välttämään yleisiä vikamuotoja, mukaan lukien halkeilua. Perimmäisenä tavoitteena on, että konesuunnittelijat voivat minimoida hitsaustarpeen ja vähentää osien määrää yrityksen mukaan. Yritys korostaa, että hitsausvolyymin vähentäminen lisää rakenteellista lujuutta ja miehistön suojaa samalla kun alentaa tuotantokustannuksia. Alkaen hyvin todistetusta 5083-H131-seoksesta yritys kehitti prosessin kylmämuovausosille, joiden taivutuskulma oli 90 astetta jyvillä ja niiden poikki, ja siirtyi sitten monimutkaisempiin materiaaleihin, esimerkiksi seoksiin 7017, 7020 ja 7085, saavuttaa myös hyviä tuloksia.
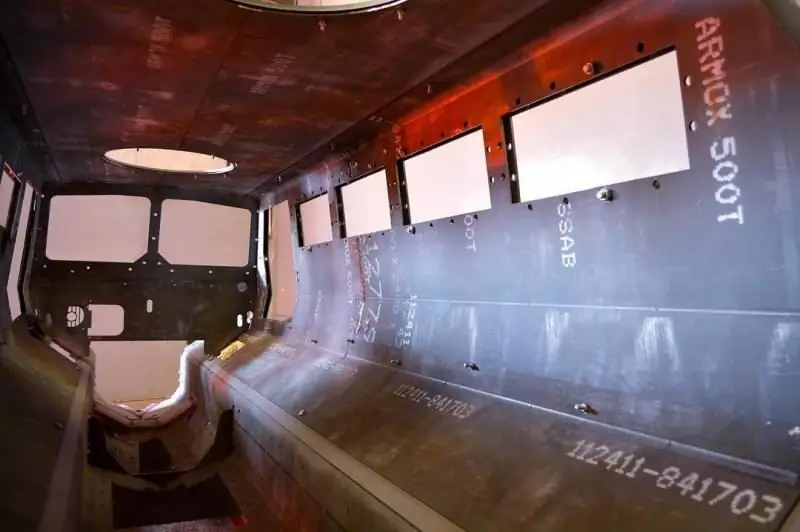
Keramiikka ja komposiitit
Useita vuosia sitten Morgan Advanced Materials ilmoitti kehittäneensä useita SAMAS -panssarijärjestelmiä, jotka koostuivat edistyneen keramiikan ja rakenteellisten komposiittien yhdistelmästä. Tuotelinja sisältää saranoidut panssarit, hajoamisen estävät vuoraukset, rakenteellisista komposiiteista tehdyt selviytymiskapselit metallirunkojen korvaamiseksi ja asumoduulien suojaamiseksi, sekä asuttuja että asumattomia. Kaikki ne voidaan mukauttaa erityisiin vaatimuksiin tai tehdä tilauksesta.
Tarjoaa STANAG 4569 -tason 2-6 suojan sekä monivaikutteisen suorituskyvyn ja painonsäästöt (yritys väittää, että nämä järjestelmät painavat puolet enemmän kuin vastaavat terästuotteet) ja mukautuvat erityisiin uhkiin, alustoihin ja tehtäviin. … Halkeamattomia vuorauksia voidaan valmistaa litteistä paneeleista, joiden paino on 12,3 kg ja jotka peittävät 0,36 m2: n alueen (noin 34 kg / m2), tai kiinteistä liittimistä, jotka painavat 12,8 kg, kun 0,55 m2 (noin 23,2 kg / m2).
Morgan Advanced Materialsin mukaan uusiin ja olemassa olevien alustojen modernisointiin suunniteltu lisäpanssari tarjoaa samat ominaisuudet puolet painosta. Patentoitu järjestelmä tarjoaa maksimaalisen suojan monenlaisia uhkia vastaan, kuten pieniä ja keskikokoisia aseita, improvisoituja räjähteitä (IED) ja rakettivetoisia kranaatteja, sekä monivaikutteista suorituskykyä.
Ase-moduuleille tarjotaan "puolijärjestelmäinen" panssarijärjestelmä, jolla on hyvä korroosionkestävyys (ilma- ja merisovellusten lisäksi), ja se säästää painoa ja minimoi painopisteen ongelmat, toisin kuin teräs, se aiheuttaa vähemmän sähkömagneettisia yhteensopivuusongelmia.
Ase -moduulien suojaaminen on erityinen ongelma, koska ne ovat houkutteleva kohde, koska niiden käytöstä poistaminen heikentää merkittävästi miehistön tilanhallintaa ja ajoneuvon kykyä käsitellä lähellä olevia uhkia. Heillä on myös herkkä optoelektroniikka ja haavoittuvat sähkömoottorit. Koska ne asennetaan yleensä ajoneuvon yläosaan, panssaroinnin tulisi olla kevyttä, jotta painopiste pysyisi mahdollisimman alhaalla.
Ase -moduulien suojausjärjestelmä, joka voi sisältää panssaroitu lasi ja yläosan suoja, on täysin kokoontaitettava, kaksi ihmistä voi koota sen uudelleen 90 sekunnissa. Komposiitti -selviytymiskapselit on valmistettu siitä, mitä yritys kuvailee”ainutlaatuisiksi kestäviksi materiaaleiksi ja polymeerivalmisteiksi”, ne tarjoavat sirpaleiden suojan ja voidaan korjata kentältä.
Sotilaan suojelu
3M Ceradynen kehittämä SPS (Soldier Protection System) -järjestelmä sisältää kypärät ja suojapanssareita integroidulle päänsuojajärjestelmälle (IHPS) ja VTP: lle (elintärkeä vartalon suojaus). pienaseet) SPS -järjestelmässä.
IHPS -vaatimukset sisältävät kevyemmän painon, passiiviset kuulonsuojaimet ja parannetut tylpät iskusuojat. Järjestelmä sisältää myös lisävarusteita, kuten komponentin, joka suojaa sotilaan alaleukaa, suojavisiirin, pimeänäkölasien kiinnittimen, ohjaimet esimerkiksi taskulampulle ja kameralle sekä modulaarisen luodinsuojan. Sopimus, jonka arvo on yli 7 miljoonaa dollaria, sisältää noin 5300 kypärän toimittamisen. Tällä välin 36 miljoonan dollarin sopimuksen puitteissa toimitetaan yli 30000 ESAPI -sarjaa - kevyempiä lisävarusteita haarniskoille. Molempien sarjojen tuotanto alkoi vuonna 2017.
Myös SPS -ohjelman puitteissa KDH Defense valitsi Honeywellin SPECTRA SHIELD- ja GOLD SHIELD -materiaalit viiteen osajärjestelmään, mukaan lukien SPS -hankkeeseen toimitettava Torso- ja Extremity Protection -alijärjestelmä. TEP -suojajärjestelmä on 26% kevyempi, mikä vähentää SPS -järjestelmän painoa 10%. KDH käyttää UHMWPE -kuituun perustuvaa SPECTRA SHIELD: tä ja aramidikuituihin perustuvaa GOLD SHIELD: tä omissa tuotteissaan tätä järjestelmää varten.
SPECTRA -kuitu
Honeywell käyttää patentoitua polymeerikuidun kehruu- ja vetoprosessia upottaakseen UHMWPE -raaka -aineen SPECTRA -kuituun. Tämä materiaali on painoltaan 10 kertaa vahvempi kuin teräs, sen ominaislujuus on 40% suurempi kuin aramidikuidun, sen sulamispiste on korkeampi kuin tavallisella polyeteenillä (150 ° C) ja kulutuskestävyys on suurempi kuin muilla polymeereillä. esimerkiksi polyesteri.
Vahvalla ja jäykällä SPECTRA -materiaalilla on suuri muodonmuutos murtumassa, eli se venyy erittäin voimakkaasti ennen murtumista; Tämä ominaisuus mahdollistaa suuren iskuenergian absorboimisen. Honeywell väittää, että SPECTRA -kuitukomposiitit toimivat erittäin hyvin suurilla nopeuksilla, kuten kivääriluoteilla ja iskuaalloilla. Yhtiön mukaan:”Edistynyt kuitu reagoi iskuun poistamalla nopeasti liike -energiaa iskualueelta … sillä on myös hyvä tärinänvaimennus, hyvä toistuvien muodonmuutosten kestävyys ja kuitujen erinomaiset sisäiset kitkaominaisuudet sekä erinomainen kemikaalien kestävyys, vettä ja UV -valoa."
SHIELD -tekniikassaan Honeywell levittää yhdensuuntaisia kuituja ja yhdistää ne yhteen kyllästämällä ne edistyksellisellä hartsilla yksisuuntaisen nauhan luomiseksi. Tämän jälkeen tämän nauhan kerrokset asetetaan ristiin haluttuihin kulmiin ja tietyssä lämpötilassa ja paineessa, juotetaan komposiittirakenteeseen. Pehmeitä pukeutumissovelluksia varten se on laminoitu kahden kerroksen ohuen ja joustavan läpinäkyvän kalvon väliin. Koska kuidut pysyvät suorina ja yhdensuuntaisina, ne hajottavat iskuenergiaa tehokkaammin kuin jos ne olisi kudottu kudottuun kankaaseen.
Short Bark Industries käyttää myös SPECTRA SHIELD: tä SPS TEP -järjestelmän BCS (ballistic Combat Shirt) -henkivartijalla. Short Bark on erikoistunut pehmeään suojaan, taktisiin vaatteisiin ja asusteisiin.
Honeywellin mukaan sotilaat valitsivat näistä materiaaleista valmistetut suojaelementit sen jälkeen, kun he olivat osoittaneet ylivoimaista suorituskykyä aramidikuitukollegoihinsa nähden.