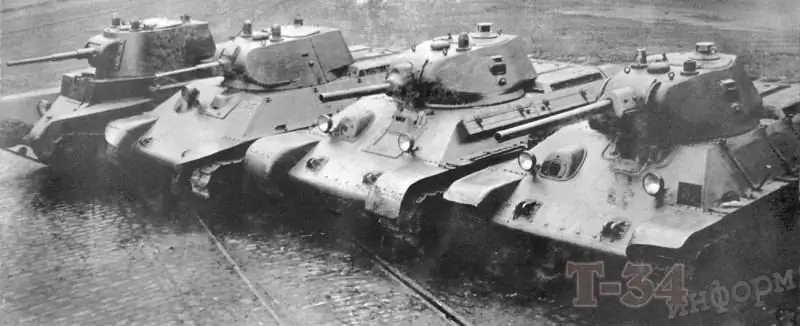
Sotaa odotellessa
Neuvostoliiton 1920- ja 1930 -luvun säiliöntuotantoon liittyvät ongelmat, jotka liittyivät pääasiassa teollisuuden puutteeseen, selitettiin osittain panssaroidun teollisuuden viivästymisellä. Vuoden 1932 alussa vain kaksi suunnitellusta neljästä yrityksestä pystyi sulattamaan ja rullaamaan panssaroita. Nämä olivat Izhoran ja Mariupolin tehtaat. Tuotantonopeutta koskevien liian korkeiden vaatimusten vuoksi (tämä oli merkki tuosta ajasta) nämä tehtaat jäivät kroonisesti suunnitelmien taakse. Joten yhdessä maan vanhimmista yrityksistä, Izhoran tehtaalla Kolpinon kaupungissa, he pystyivät hallitsemaan vuodessa vain 38% suunnitelmasta ja Mariupolissa Ilyichin tehtaalla - vain neljänneksen. Tämä johtui suurelta osin monimutkaisten sementoitujen heterogeenisten panssarien valmistuksesta, jotka he tiesivät tehdä maassamme vuodesta 1910 lähtien. Samantyyppistä panssaria vaadittiin kestämään teräväpäisiä ammuksia ja luoteja, joita tavallinen homogeeninen keskikokoinen ja matala kovuus ei tarjonnut. Tuolloin sementoitu panssari jaettiin kahteen laatuun: matalakarkaistu yksipuolisesti sementoitu riittävän kovalla selkäpuolella ja toisessa versiossa keskikova takapuoli. Pohjimmiltaan tällaisten "voileipien" valmistukseen tarvittiin kromi-molybdeeniä ja kromi-nikkeli-molybdeeniterästä, mikä vaati harvoja maahantuotuja ferroseoslisäaineita. Näiden terästen tärkein seosaine oli kromi (1, 5-2, 5%), joka edistää intensiivistä hiiltymistä ja kovettuneen kerroksen kovuuden saavuttamista sammutuksen jälkeen. Yritys käyttää kotimaista mangaania ja piitä kotelokarkaistua terästä tuodun kromin sijasta tuotti negatiivisen tuloksen. Kun seostettiin mangaanilla, paljastui, että teräs on altis rakeiden kasvulle hiiltymislämpötilassa (920-950 celsiusastetta), etenkin pitkillä valotuksilla, jotka vaaditaan kovettamiseen suuressa syvyydessä. Sementin aikana ylikuumentuneen hiiltyneen kerroksen korjaaminen tuotti merkittäviä vaikeuksia ja liittyi tarpeeseen soveltaa moninkertaista uudelleenkiteytystä, mikä aiheutti merkittävän hiilihapotuksen sementoidussa kerroksessa ja levyjohtimissa ja oli myös taloudellisesti kannattamatonta. Siitä huolimatta, 30 -luvun alkuun asti, sementoitua panssaria käytettiin sekä ilmailussa että säiliörakennuksessa. Lentokoneissa jopa 13 mm paksuisia panssarilevyjä sementoitiin, kuten säiliön panssaria jopa 30 mm. Kehitettiin myös luodinkestävää 20 mm: n sementoitua panssaria, joka ei ylittänyt kokeellista kehitystä. Tällaisen panssarin piti ehdottomasti olla massiivinen, mikä vaati vain jättimäisiä resursseja tuotannon kehittämiseen.
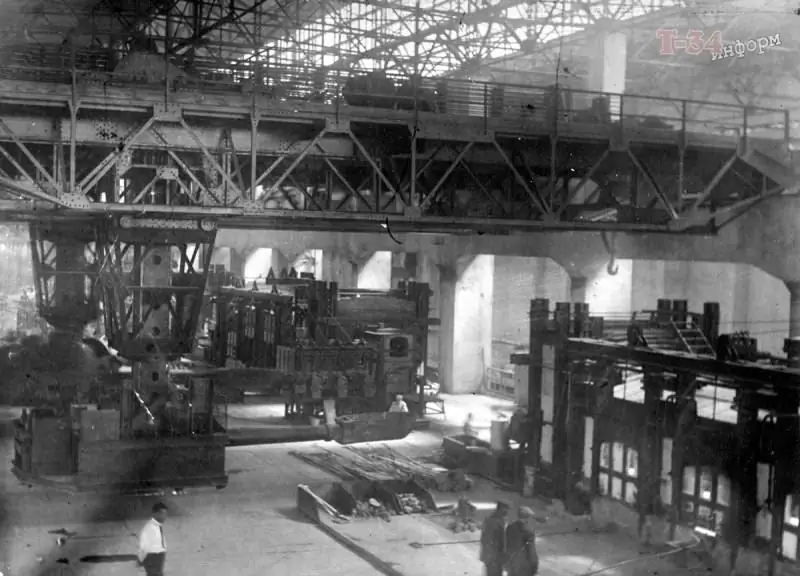
Huolimatta tällaisista vaikeuksista kovetetun panssarin tuotannossa, T-28-säiliön runko oli lähes kokonaan valmistettu siitä. Mutta vähitellen kotimainen teollisuus luopui panssarilevyjen sementtitekniikoista, suurelta osin erittäin korkeiden hylkäysten vuoksi. Kun otetaan huomioon hallituksen ja erikoistuneiden kansankomissaarien vaatimat tuotantosuunnitelmat, tämä ei ollut ollenkaan yllättävää. Izhoran tehdas siirtyi ensimmäisenä uuteen panssariin, kun hän oli hallinnut korkean kovan kromi-piipitoisen mangaanipanssarin "PI" sulatuksen. Mariupolissa he hallitsivat heterogeenisen mangaanin "MI". Maa siirtyi vähitellen omaan kokemukseensa panssarien suunnittelussa. Siihen asti se perustui ulkomaisiin tekniikoihin (pääasiassa brittiläiseen). Kieltäytyminen sementin panssarista teki levyistä paksumpia samalla panssarivastuksella. Joten 10- ja 13 mm: n sementtihaarniskan sijasta T-26-runko oli hitsattava 15 mm: n Izhora-teräslevystä "PI". Tässä tapauksessa säiliö oli 800 kiloa painava. On huomattava, että siirtyminen kalliista sementoidusta teräksestä suhteellisen edullisiin homogeenisiin panssaritekniikoihin osoittautui erittäin hyödyllisiksi sodan aikana. Jos näin ei olisi tapahtunut ennen sotaa, kalliiden panssaroiden sulatuksen ja valssauksen kehittäminen olisi epätodennäköistä, kun otetaan huomioon yritysten evakuointi vuosina 1941-1942.
Sotaa edeltävistä vuosista lähtien päärooli uuden tyyppisten panssarien etsimisessä ja tutkimuksessa oli "panssari-instituutissa" TsNII-48, joka tunnetaan nyt nimellä NRC "Kurchatov Institute"-TsNII KM "Prometheus". Insinöörien ja tutkijoiden TsNII-48-tiimi määritteli kotimaisen panssariteollisuuden pääsuunnat. Sotaa edeltäneellä viime vuosikymmenellä 20-50 mm: n kaliipereiden panssaroivien tykistöjen ilmestyminen ulkomaille tuli vakavaksi haasteeksi. Tämä pakotti kehittäjät etsimään uusia reseptejä säiliön panssarin keittämiseen.
8C: n syntymä
Vaihda teräväpäisiä ammuksia ja luoteja kestävä sementoitu panssari kevyissä ja keskipanssaroiduissa ajoneuvoissa vain erittäin kovaa terästä. Kotimaiset metallurgit hallitsivat tämän onnistuneesti. Panssaroitujen ajoneuvojen rungot BA-10, kevyet säiliöt T-60 (panssarin paksuus 15 mm, edestä-35 mm), T-26 (panssarin paksuus 15 mm) ja tietysti keskikokoiset säiliöt T-34 (panssarin paksuus 45 mm). Saksalaisilla oli myös korkean kovuuden panssari etusijalla. Itse asiassa kaikista haarniskoista (alkaen jalkaväen kypäristä ja päättyen ilmailun suojarakenteisiin) tuli lopulta korkea kovuus, joka korvasi sementoidun. Ehkä vain raskailla KV: llä oli varaa keskikovaan panssariin, mutta tämä joutui maksamaan arkkien suuremman paksuuden ja säiliön lopullisen massan kanssa.
8C-panssariteräksestä, joka oli T-34-säiliön tykinvastaisen puolustuksen perusta, tuli todellinen kotimaisten metallurgien luovuuden kruunu. On huomattava, että 8C-panssarin valmistus ennen sotaa ja Suuren isänmaallisen sodan aikana oli kaksi vakavasti erilaista prosessia. Jopa Neuvostoliiton sotaa edeltäneelle teollisuudelle 8C: n tuotanto oli monimutkainen ja kallis prosessi. He pystyivät hallitsemaan sen onnistuneesti vain Mariupolissa. 8C: n kemiallinen koostumus: C - 0,22-0,28%, Mn - 1,0-1,5%, Si - 1,1-1,6%, Cr - 0,7-1,0%, Ni - 1,0-1,5%, Mo - 0,15-0,25%, P - alle 0,035% ja S - alle 0,03%. Sulatusta varten tarvittiin avotakka-uuneja, joiden kapasiteetti oli jopa 180 tonnia ja jotka kaatoivat tulevaisuuden panssarin suhteellisen pieniin, 7,4 tonnin muotteihin. Nestemäisen seoksen hapetus (ylimääräisen hapen poistaminen) uunissa suoritettiin kalliilla diffuusiomenetelmällä käyttäen hiiltä tai piitä. Valmis harko otettiin muotista ja rullattiin, mitä seurasi hidas jäähtyminen. Tulevaisuudessa tuleva haarniska lämmitettiin jälleen 650-680 asteeseen ja jäähdytettiin ilmassa: se oli korkea loma, jonka tarkoituksena oli antaa teräkselle plastisuutta ja vähentää haurautta. Vasta sen jälkeen teräslevyt voitiin käsitellä mekaanisesti, koska seuraava kovettuminen ja alhainen karkaisu 250 asteessa tekivät siitä liian kovan. Itse asiassa 8C: n viimeisen karkaisumenettelyn jälkeen oli vaikeaa tehdä mitään muuta kuin hitsata runko siitä. Mutta täälläkin oli perustavanlaatuisia vaikeuksia. Merkittäviä sisäisiä hitsausjännityksiä, jotka johtuvat 8C -panssarimetallin alhaisesta sitkeydestä, erityisesti sen huonolaatuisuudesta, johtavat halkeamiin, jotka usein lisääntyivät ajan myötä. Halkeamia saumojen ympärille voi muodostua jopa 100 päivää säiliön valmistuksen jälkeen. Tästä tuli todellinen vitsaus Neuvostoliiton säiliörakennuksessa sodan aikana. Ja ennen sotaa tehokkain tapa estää halkeamien muodostuminen 8C-panssarin hitsauksen aikana oli hitsausalueen esilämmityksen käyttö 250-280 asteen lämpötilaan. Tätä tarkoitusta varten TsNII-48 kehitti erityisiä induktoreita.
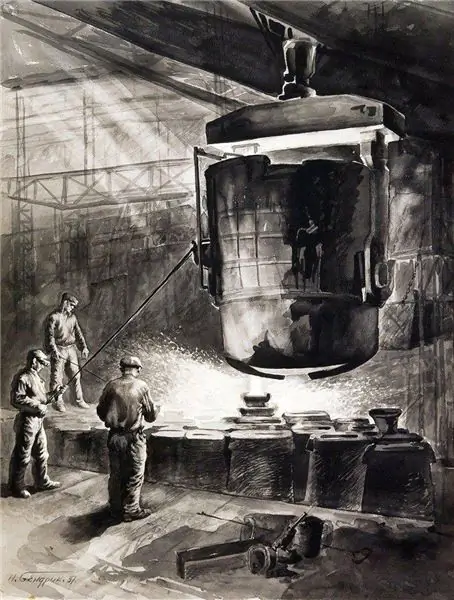
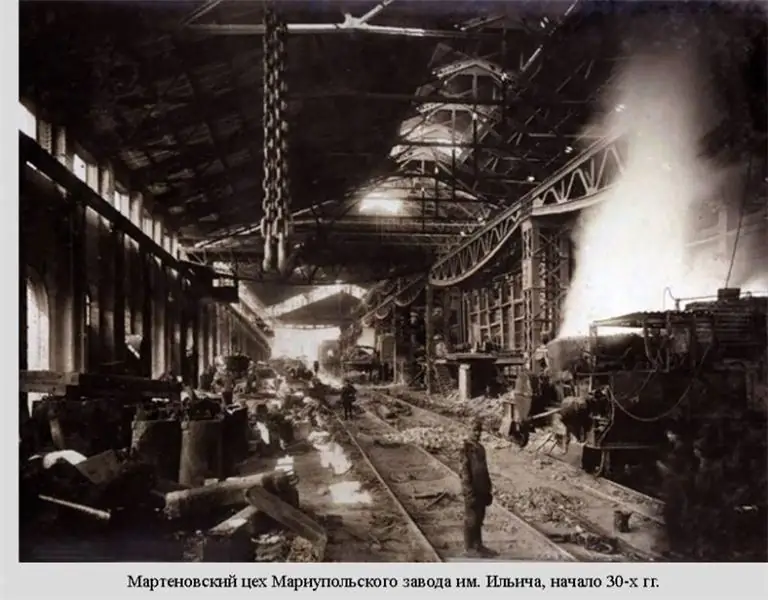
8C ei ollut ainoa teräslaatu T-34-panssaroille. Jos mahdollista, se vaihdettiin muihin halvempiin lajikkeisiin. Ennen sotaa TsNII-48 kehitti 2P-rakenteellisia panssaroita, joiden valmistus säästää merkittävästi energiaa ja yksinkertaistaa arkin rullaamista. 2P: n kemiallinen koostumus: C - 0,23-0,29%, Mn - 1,2-1,6%, Si - 1,2-1,6%, Cr - alle 0,3%, Ni - alle 0, 5%, Mo - 0,15-0,25%, P - alle 0,035% ja S - alle 0,03%. Kuten näette, suurimmat säästöt olivat niukalla nikkelillä ja kromilla. Samaan aikaan erittäin tiukat toleranssit fosforin ja rikin läsnäololle pysyivät muuttumattomina 2P: n osalta, mikä oli tietenkin vaikeaa saavuttaa erityisesti sodan aikana. Kaikista yksinkertaistuksista huolimatta 2P -teräksestä valmistetut rakenteelliset panssarit kävivät edelleen lämpökäsittelyllä - sammutuksella ja korkealla karkaisulla, mikä kuormitti merkittävästi säiliöiden kriittisempien panssariosien lämpökäsittelyyn tarvittavia lämpölaitteita ja lisäsi myös merkittävästi tuotantosykliä. Sodan aikana TsNII-48-asiantuntijat pystyivät kehittämään tekniikoita vastaavien terästen hankkimiseksi, joiden tuotanto vapautti resursseja 8C-panssarille.