Sota tunnetaan parhaana kehityksen moottorina. Neuvostoliiton säiliöteollisuus teki huimaavan laadullisen harppauksen vain muutamassa sodan vuodessa. Tämän todellinen kruunu olivat IS -sarjan säiliöt.
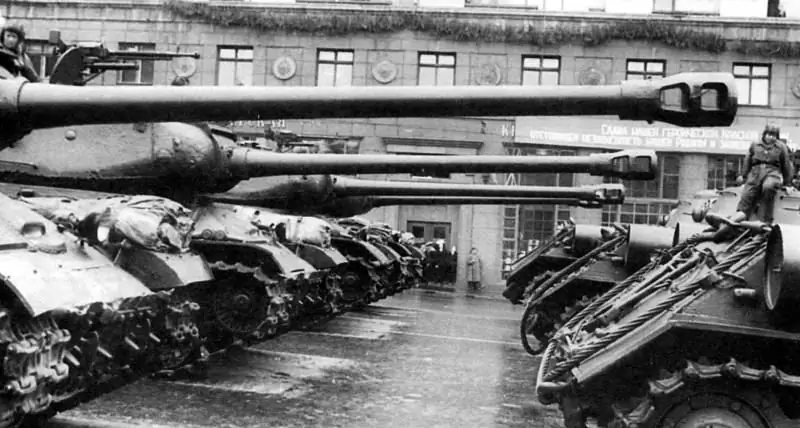
Magnitogorskin reseptit
Edellisessä osassa tarina käsitteli 70 litran kovakestävää valettua panssaria, jota käytettiin IS-säiliöiden torneissa. TsNII-48: n panssarikehittäjät eivät olleet kaukana ensimmäisestä kokemuksesta raskaiden säiliöiden suojauksen luomisessa.
Ennen Kursk Bulgea, josta tuli katalysaattori kotimaisen raskaan säiliön rakentamisen kehittämiselle, modernisoinnin päätavoite oli KV -säiliö. Aluksi kaiken työn tarkoituksena oli vähentää niukkojen seostavien lisäaineiden osuutta panssarin koostumuksessa. Jopa TsNII -48: n nimi keksi sopivan - taloudellisesti seostetun teräksen. FD-7954-tuotemerkin alkuperäinen panssari, jolla KV-säiliö tuli Suuri isänmaallinen sota, sisälsi teknisten vaatimusten mukaan jopa 0,45% molybdeenia, 2,7% nikkeliä ja kromia.
Vuoden 1941 loppuun mennessä ryhmä tutkijoita Andrei Sergeevich Zavyalovin johdolla panssaroidussa instituutissa loi reseptin teräkselle FD -6633 tai 49C, jossa molybdeeni tarvitsi enintään 0,3%, kromia - jopa 2,3%ja nikkeliä. enintään 1,5%. Kun otetaan huomioon, että KV -sarjan säiliöitä vuoden 1941 toiselta puoliskolta 1943 kerättiin noin 4 tuhatta kappaletta, voidaan kuvitella todellisten säästöjen määrä metalliseoksista.
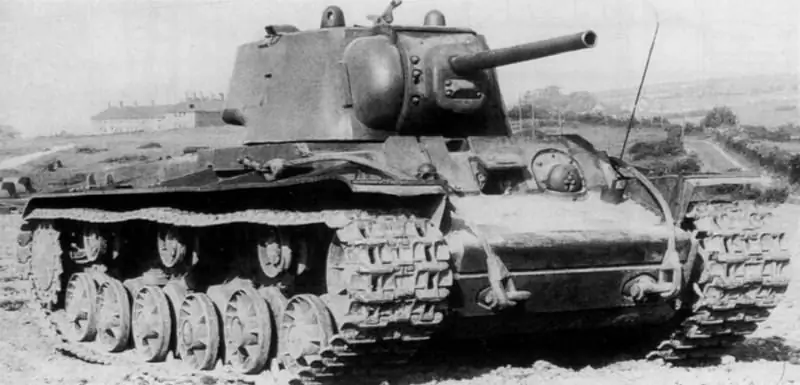
Menestyksen salaisuus
Metallurgien menestyksen salaisuus on panssaroiden kuitumurtuman muodostumisen parametrien tutkimuksessa - ammuksen kestävyyden pääparametri. Kävi ilmi, että voit tehdä ilman merkittävää osaa seosaineita yksinkertaisesti muuttamalla panssarin jäähdytysnopeutta sammutuksen aikana. Mutta tämä on sanoin yksinkertaista - kuinka monta alustavaa kokeilua ja sulatusta metallurgien oli tehtävä, vain nyt luokiteltu arkisto voi kertoa.
Magnitogorskin metallurgisessa tehtaassa vuonna 1941 saatiin ensimmäiset 49C-teräksen prototyypit, jotka eivät olleet huonompia kuin perinteiset "ennen sotaa" -panssarit. Erityisesti 76 mm: n tykin kuoret osoittivat täyttävänsä säiliön taktiset vaatimukset. Ja vuodesta 1942 lähtien KV -sarjassa on käytetty vain panssaria, jonka nimi on 49C. On syytä muistaa, että kromin, molybdeenin ja nikkelin kulutus on vähentynyt merkittävästi.
Uusien panssarikoostumusten etsiminen raskaisiin laitteisiin ei päättynyt tähän. Vuonna 1942 teräs GD-63-3”hitsattiin” täysin ilman niukkaa kromia ja nikkeliä. Jossain määrin nikkeli korvattiin mangaanilla - sen osuus kasvoi yli kolme kertaa (jopa 1,43%). Uuden panssarin prototyyppejä ammuttiin. Ja ne osoittautuivat sopiviksi massakäyttöön KV: n suunnittelussa. Mutta Klim Voroshilov -säiliöt keskikovilla panssaroilla olivat eläkkeellä. Ja raskaiden ajoneuvojen sijalle tuli”Joseph Stalin” -autot, joilla oli korkea kovuuspanssari.
Valssattu panssari 51C
Jos 70-litrainen panssari IS-2-tornille voitaisiin heittää, tämä temppu ei toiminut säiliön rungon osien kanssa. Täällä insinöörit kohtasivat kaksi ongelmaa kerralla - erittäin kovan, erittäin paksun panssarin luominen ja tarve hitsata se valmiiksi rungoksi.
Kaikki asiasta kiinnostuneet ovat luultavasti jo tietoisia T -34 -panssarin hitsauksen aiheuttamista ongelmista - hitsien alueella on suuri halkeamien todennäköisyys. IS-2 ei ollut poikkeus. Ja sen runko oli alun perin tarkoitus keittää lopulta lämpökäsitellyistä osista.
Ymmärtäessään, millaisia vaikeuksia ja vaaroja tällainen tekninen ratkaisu toisi sotilasoperaatioon, TsNII-48-asiantuntijat muuttivat säiliön tuotantosykliä. Tämän seurauksena vuonna 1943 Uralin raskaan koneenrakennustehtaalla ja Tšeljabinskin tehtaalla nro 200 IS-2-runko päätettiin keittää panssarilevyistä, jotka olivat kulkeneet vasta korkean loman vierittämisen jälkeen. Eli raskaan säiliön runko koottiin "raakateräksestä". Tämä pienensi huomattavasti hitsausvirheitä 51C-kovakantisessa valssatussa panssarissa.
Lopullinen lämpökäsittely kuumentamalla ennen sammutusta suoritettiin jo säiliön hitsatulla rungolla, kun se oli aiemmin vahvistettu sisäisillä tukilla. Ruumista pidettiin uunissa kolme tuntia. Ja sitten ne siirrettiin erityislaitteilla veden sammutusastiaan ja pidettiin siinä 15 minuuttia. Lisäksi veden lämpötila jäähdytyssäiliössä nousi 30 asteesta 55 asteeseen. Veden poistamisen jälkeen ruumiin pintalämpötila oli 100-150 ° С. Eikä siinä kaikki.
Sammutuksen jälkeen keho altistettiin välittömästi matalalle karkaisulle kiertouunissa 280-320 ° C: n lämpötilassa pitäen kiinni tämän lämpötilan saavuttamisen jälkeen 10-12 tuntia. 70L panssarin valettujen tornien matala karkaisu suoritettiin samalla tavalla. Mielenkiintoista on, että halkeamien hallinta kokeellisissa IS-2-rungoissa kesti neljä kuukautta, kun ensimmäiset tuotantosäiliöt lähtivät tehtaan porteilta.
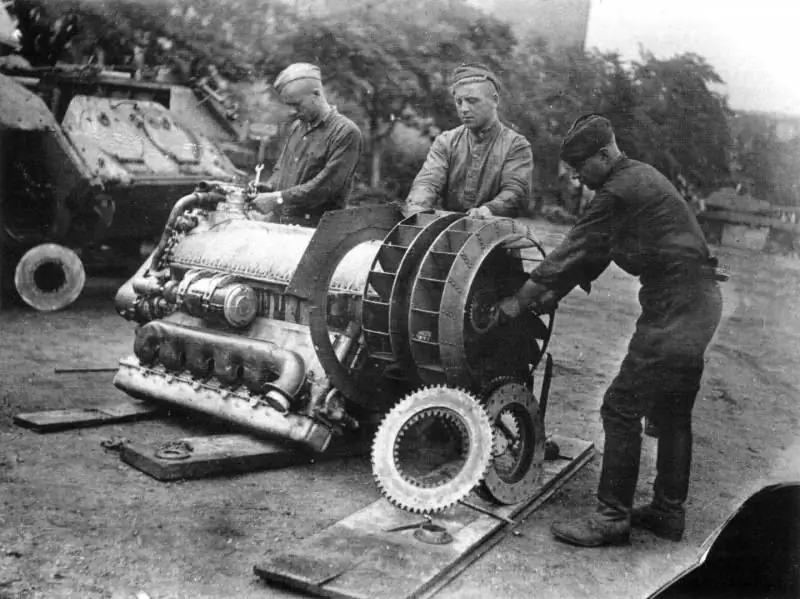
Kemiallinen koostumus
Mikä oli 51C-valssattu panssari, josta tuli IS-2: n, ISU-122: n ja ISU-152: n tärkein? Se on syväkarkaisuteräs suurille panssaripaksuuksille, ja sen kemiallinen koostumus (%) on seuraava:
C 0, 18-0, 24
Mn 0, 70-1, 0
Si 1, 20-1, 60
Cr 1, 0-1, 5
Ni 3,0-3,8
Mo 0, 20-0, 40
P ≤0,035
S ≤0,035.
Verrattuna valettuun panssariin 70L, 51C -valssatussa teräksessä oli enemmän molybdeeniä ja nikkeliä, mikä takaa kovettavuuden kasvun jopa 200 mm. Kun raskaiden säiliöiden runkoja ammuttiin 88 mm: n kuorilla, kävi ilmi, että korkean kovuuden panssari oli kestävyydeltään paljon parempi kuin sen keskikovuusiset edeltäjät. Valssatun panssarin 51C sijoittaminen ratkaistiin välittömästi.
Älykäs hitsaus
Tärkeä panos IS -sarjan säiliöiden panssarituotannon kehittämisen onnistumiseen annettiin teräksen automaattisella hitsauksella vuokerroksen alle. Koska koko säiliöpanssarirungon valmistusprosessia oli mahdotonta siirtää tällaiseen hitsaukseen vuoden 1944 alussa, insinöörit keskittyivät laajimpien ja mekaanisesti kuormitettujen saumojen automatisointiin.
Tšeljabinskin tehtaalla nro 200 raskaan IS-2-säiliön rungon kokoamisprosessissa vain 25% kaikista hitsauksista voitaisiin automatisoida. Vuoden 1944 puoliväliin mennessä Tankograd pystyi automatisoimaan 18% kaikista mahdollisista 25% hitsauksista. IS-2-raskaan säiliön rungon hitsattujen saumojen kokonaispituus oli 410 juoksevaa metriä, josta 80 juoksumattoa suoritettiin automatisoidulla hitsausmenetelmällä.
Tämä tulos on johtanut merkittäviin säästöihin niukoissa resursseissa ja sähkössä. Oli mahdollista vapauttaa jopa 50 pätevää manuaalista hitsaajaa (heidän työvoimakustannuksensa olivat 15 400 työtuntia) ja säästää 48 000 kilowattituntia sähköä. Elektrodien (noin 20000 kg, austeniittiset - 6000 kg), hapen (1440 kuutiometriä) vähentynyt kulutus.
Myös hitsaukseen käytetty aika on lyhentynyt merkittävästi. Esimerkiksi pohjan ja tornilaatikon hitsaaminen sivuille kuusitoista metrin saumalla kesti 9,5 työtuntia manuaalitilassa ja vain 2. Sauma, joka on samanpituinen ja joka yhdistää pohjan säiliön rungon sivuille automaattitilassa 3 työtuntia (käsikirjassa heti 11, 4). Samaan aikaan korkeasti koulutetut hitsaajat voitaisiin korvata ammattitaidottomilla työntekijöillä automaattisessa hitsauksessa.
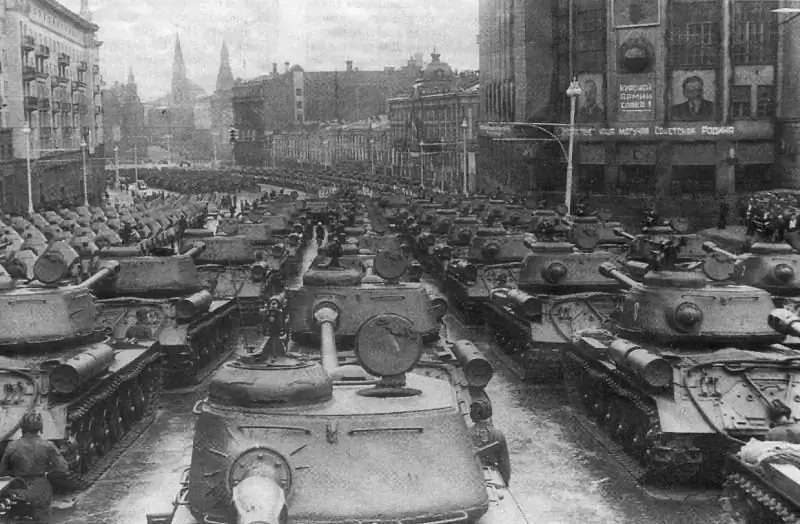
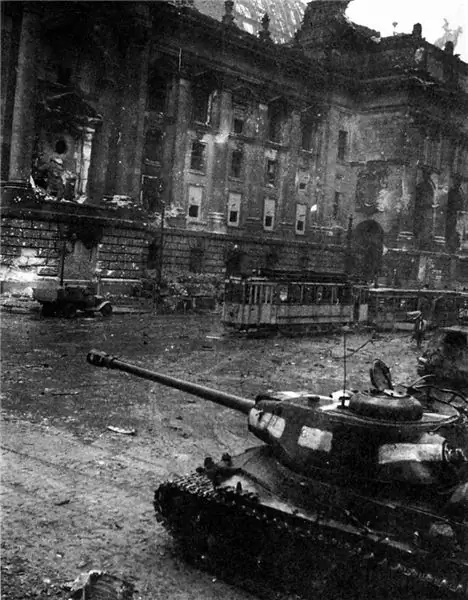
Uralin SAG: t
Neuvostoliiton säiliöteollisuuden tutkija, historiantieteiden ehdokas Zapari Vasily Vladimirovich Venäjän tiedeakatemian Uralin haaratoimiston historian ja arkeologian instituutista yhdessä teoksessaan kuvaa yksityiskohtaisesti Uralin panssaroituja automaattisia hitsausyksiköitä rungon tuotanto.
Yleisin oli ACC -tyyppinen rynnäkkökivääri, jossa oli Bushtedt -pää. Uralmashissa oli kahdeksan tällaista asennusta. Langansyöttönopeus tässä koneessa riippui kaaren jännitteestä. Se vaati 5 yksikköä, mukaan lukien 3 kinemaattista sähkömoottoria ja 1 moottorigeneraattorin.
Vuoden 1943 puoliväliin mennessä SA-1000-hitsauskone suunniteltiin IS-2-raskaiden säiliöiden tarpeisiin. Tai hitsauskone, jonka kapasiteetti on jopa 1000 A.
Voidakseen hallita panssarirunkojen valmistusta uudelle Tšeljabinskin raskaalle säiliölle IS-3, tehtaan insinöörit suunnittelivat vuonna 1944 laitteen "SG-2000". Tämä kone on suunniteltu toimimaan vähähiilisten hitsauslankojen kanssa, joiden halkaisija on suurempi (6-8 mm), ja sitä sovellettiin IS-3-tornin valmistuksessa. Laitteistossa oli annostelija, jolla hitsausosaan saatettiin erityinen koostumus (erilaisia ferroseoksia), jotta siinä oleva metalli hapetettiin (palautettiin). Kaikkiaan UZTM: n hitsauskaaren itsesääntelyn periaatteella luotiin vuoteen 1945 mennessä 9 kolmen tyyppistä automaattista hitsauslaitosta: "SA-1000", "SG-2000", "SAG" ("Automaattinen hitsaus pää").
Kauniimpi kuin saksalainen haarniska
Koko tarinan tulos raskaiden IS -panssarien panssarilla oli yllättävän nopea teräsreseptin kehittäminen, joka ylitti saksalaiset panssarit taktisilla ominaisuuksillaan. TsNII-48 sai karkaistavan 120 mm: n teräksen, jonka paksuus voidaan tarvittaessa lisätä 200 mm: iin.
Tästä tuli tärkein perusta sodanjälkeisen raskaan Neuvostoliiton panssariperheen kehittämiselle.